HVAC
Scroll down for links with more details on :
– Air Handling Unit and Fan Coil Unit
– Chiller Plant
– Cooling Tower
– Air Distribution and Terminal System
– Indoor Environment
– Accessibility
Central chilled water HVAC systems are commonly used for large commercial, industrial, institution and office buildings.
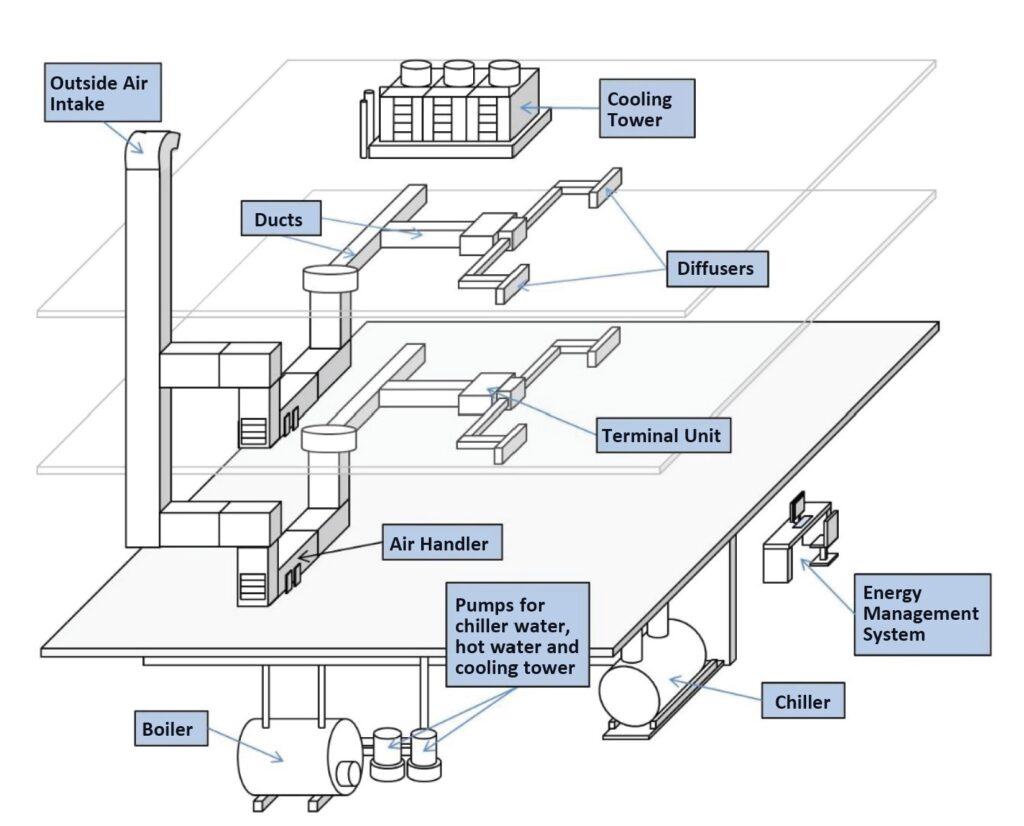
Operating and maintenance costs of these systems are often seen as the most expensive LCC expenditure. HVAC systems consume a large amount of energy monthly, often more than 50% of the total energy in commercial buildings.
Maintainability of HVAC Systems
Inadequate performance of HVAC systems has been associated with negative effects on occupants’ health and productivity, biological growth, moisture problems and high energy costs. A HVAC system is a mechanical system of which periodical system failure is inevitable; hence it is crucial that the system can be restored to its normal operable state within a given timeframe, using the prescribed practices and procedures.
The maintainability of HVAC should be considered at the outset of the planning/design stage to achieve:
- longer lifespan of systems and components,
- lower operating costs by performing at high efficiency,
- lesser unscheduled downtime, by preventing failures,
- lesser scheduled downtime, by decreasing the time required to perform a particular maintenance task (low MTTR).
Reference is made to:
- SS 553 — Code of practice for air-conditioning and mechanical ventilation in buildings
- NEA — Code of practice for control of Legionella bacteria in cooling tower
- ANSI/ASHRAE/IES Standard 90.1 — Energy standard for buildings
Testing and Commissioning
The main tests for HVAC are:
- Ductwork airtightness test
- Pipework pressure test
- Cooling tower test
- Chiller test
- AHU test
- Reliability test
ASHRAE Guideline 0 and ASHRAE Guideline 1.1 describe the procedures, methods and documentation requirements of each phase of the commissioning process for existing HVAC systems and assemblies. Performance tests are then run, and the necessary adjustments of valves, dampers and controls are made to fulfil the designed functions. Reference can be made to an acceptable standard, such as ASHRAE 111, which describes the testing, adjusting, and balancing of building HVAC systems.
In addition to commissioning tests by vendors of various equipment and components, on-site tests of individual plant/system items to be conducted include:
- Ductwork — check for tightness and vibration and operation of all movable fittings.
- Pipework — check for strength and leaks using hydrostatic tests.
- Insulation — check for integrity.
- Grilles — check for air flow rate.
- Fans — check for alignment, rotational frequency, flow rate, pressure, and capacity.
- Heat transfer coils and automatic control valves — check for water flow, pressure drop, and heat transfer on the air-side and water-side.
- Control equipment — check to ensure they are calibrated and set points adjusted.
Building owners or their designated representative should ensure that within 90 days after the date of system acceptance, the record drawings and operating/maintenance manual of the actual installation are provided, showing:
- the location and performance data of each piece of equipment
- the general configuration of the duct and pipe distribution system (including sizes)
- the terminal air or water design flow rates
- equipment size and selected options for each piece of equipment requiring maintenance
- routine maintenance action required for each piece of equipment
- air-conditioning control systems maintenance and calibration information, including wiring diagrams, schematics and control sequence descriptions
- a narrative of how each system is intended to operate, including suggested set points.
Maintenance
The planning/design team should, at the design stage, ensure that adequate access for the inspection, maintenance and repair of all components is provided. Monthly, half-yearly and annual inspections on chillers, compressors, condenser coils, chilled and condenser water pumps, water tanks, air handling units, fan coil units, motors, chemical treatment systems, electrical/electronic and mechanical controls, circuit boards, etc., should be conducted.
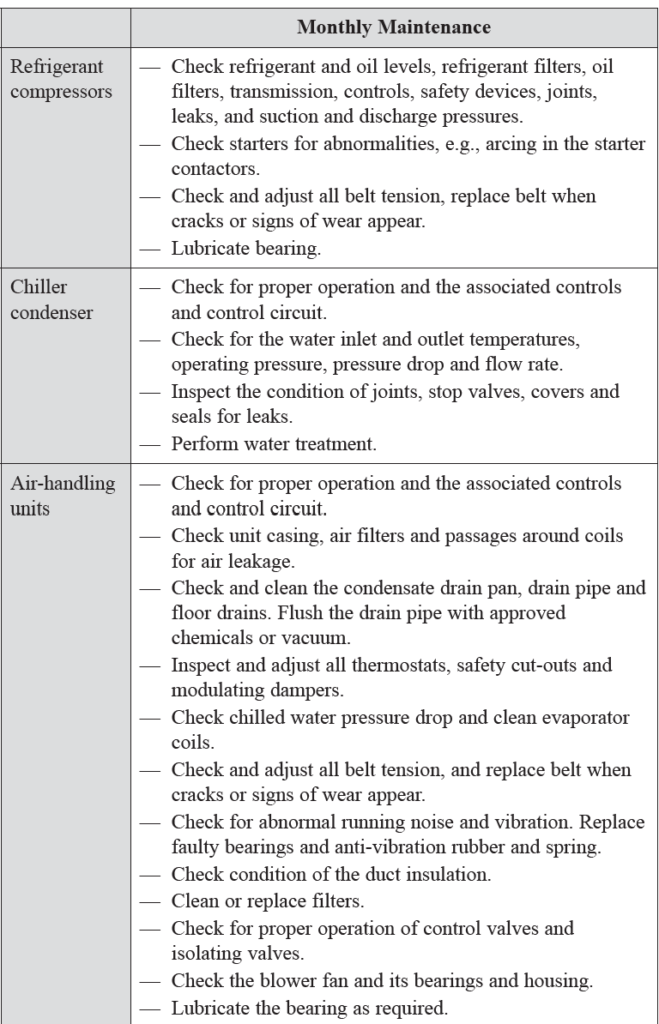
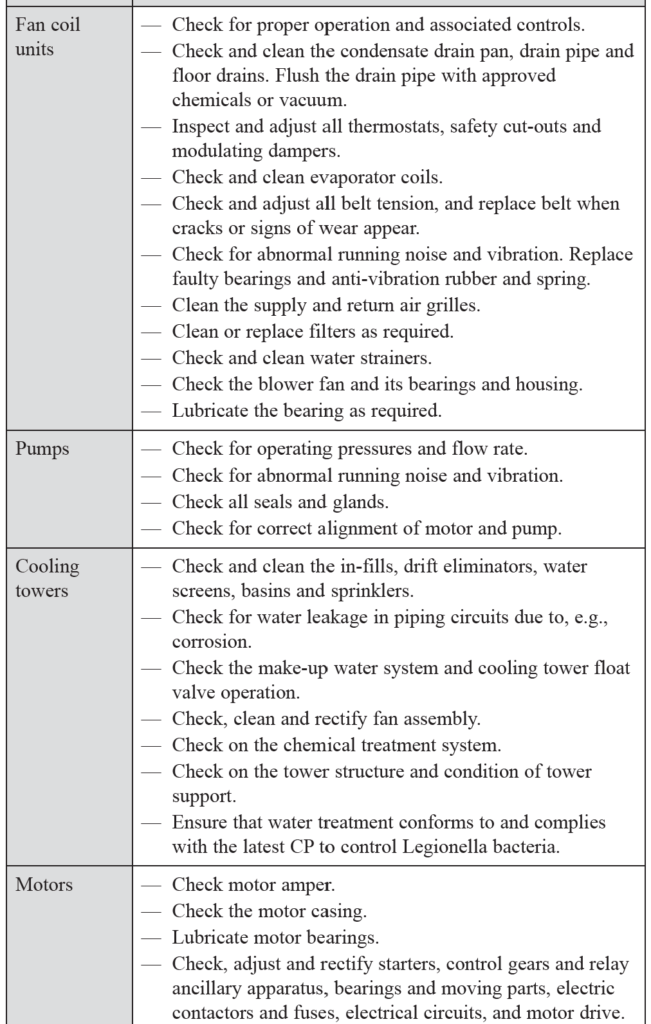
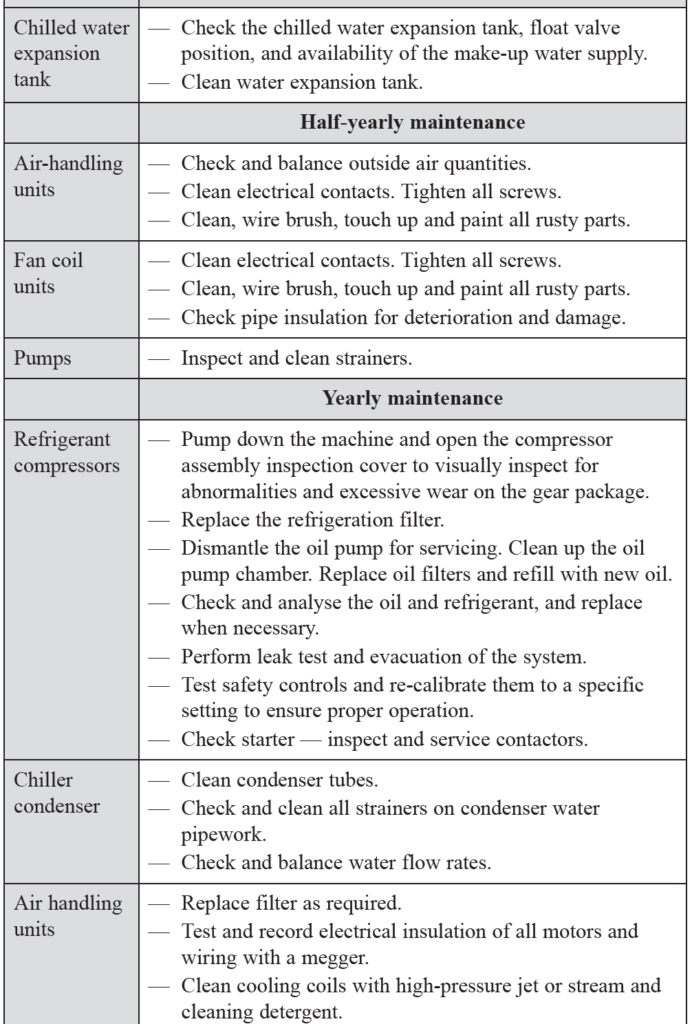
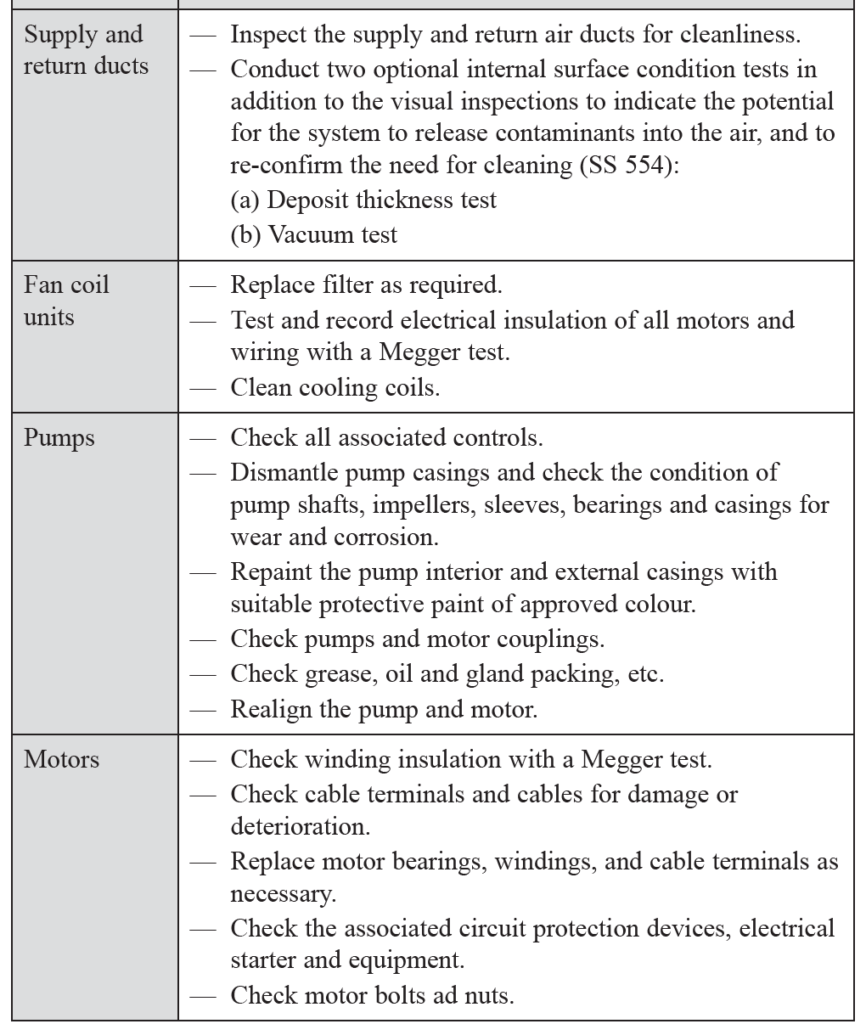
Common Defects
HVAC systems have long been blamed as a major culprit in facilities for their high-energy consumption and emission of ozone-depleting gases. Defects, such as leakages, exacerbate the problems and may further impose threats to users’ health. Various problems are found to occur in the long-term running of HVAC systems, such as mould growth in the supply air duct affecting occupants’ health, the loss of comfort, and wastage of energy. The common problem of poor humidity control is actually an indication of many major defects. Air leakage on the return duct, wrong placement or omission of sensors and short-circuiting are only a few of the reasons. It is hence crucial that before commissioning, the system specifications should be checked from time to time with the designer and manufacturer. Poorly maintained cooling towers, especially located in the direction of the air intake, may induce the fatal Legionnaires’ disease. Micro-biologically induced corrosion (MIC) can cause pitting and the very rapid loss of metallic parts. Apart from this, formicary corrosion and galvanic corrosion are also found to be common issues to a large extent.
Shortage in the air supply, accompanied by internal finishes with high total volatile organic compounds (TVOCs), can cause sick building syndrome. Overflowing of the condensate drain pan causes water stagnation that facilitates biological growth. Heat exchanger fouling and particulate deposition diminish heat transfer performance, increase pressure drops, and can cause contamination of working fluids. A ventilation system is one of the pathways to disseminating infectious diseases transmitted through the inhalation of airborne infectious particles. The risk can be reduced using dilution ventilation, directional ventilation, in-room airflow regimes, room pressure differentials, personalised ventilation and source caption ventilation, filtration, and ultraviolet germicidal irradiation (UVGI). Healthcare facilities, e.g., hospitals, should have an HVAC system with the ability to separate high-risk areas, upgrade filtration, increase ventilation to 100% outdoor air, and humidify air.
Modern HVAC systems are designed not only to meet cooling and relative humidity requirements, but to also provide equipment efficiency, envelope construction methods, and optimise system demands, in order to achieve high energy efficiency. Being a complex system, HVACs require regular maintenance to prevent mould growth in the supply air duct and ensure the precise functioning of sensors. These practices are mandatory requirements for maintaining a healthy and comfortable indoor environment in buildings. The HVAC system defects are categorised according to issues concerning (a) the chiller plant (e.g. compressor problem, insufficient/slow cooling, chilled water pipe and condenser pipe leakage and condensation); (b) cooling towers (e.g. biological fouling and Legionella outbreak); (c) air handling unit (e.g. air distribution system efficiency and noisy operation/excessive vibration); (d) air distribution and terminal systems (e.g. dirty and mouldy ductwork and filter media choked at the air terminal); and e) indoor environment. Accessibility issues concerning the HVAC system is also added as an important factor to consider when designing the HVAC system. As periodic system failure is expected in a HVAC system, the restoration of the system to its normal operable state in a given timetable is important. Disregarding preventive maintenance for components which require energy resources (e.g. chillers and fans) will reduce the HVAC’s service life, resulting in untimely HVAC component replacement, and spark a surge in operational costs. The maintainability of HVAC systems could be considered during the design stage to ensure adequate access for the inspection, maintenance and repair of all components.
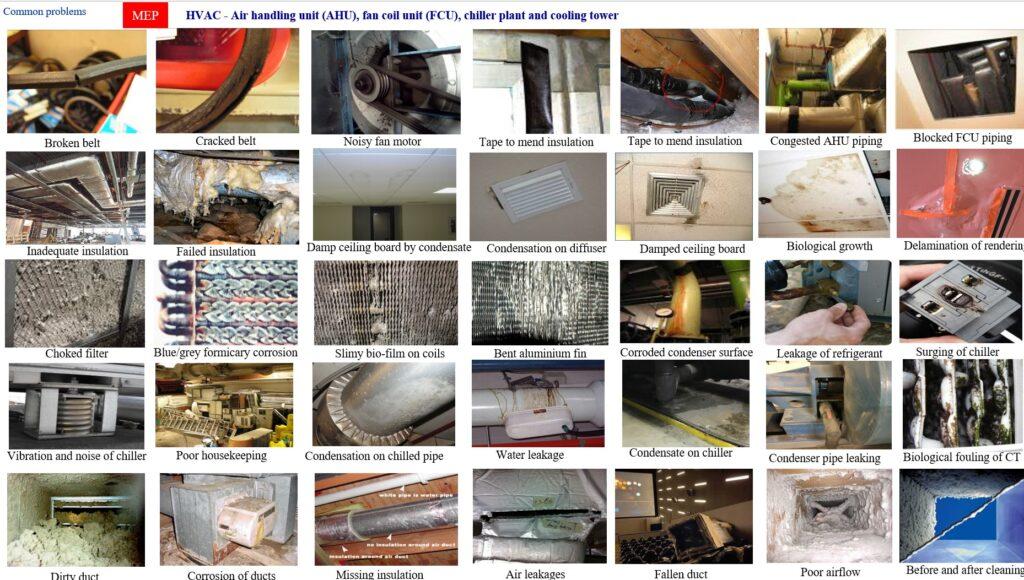
NOTE: All designs, construction, installation, testing and commissioning (T&C), operation and maintenance (O&M) of air conditioning and mechanical ventilation (ACMV) Systems must comply with the Code of Practice for ACMVs in Buildings, SS 553. For the energy efficiency standard for building services and equipment, SS 530 must be adopted.

Air Handling Unit and Fan Coil Uni


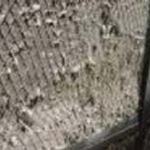
Air Distribution and Terminal Systems


Accessibility Considerations in HVAC System
References
- SS 553 — Code of practice for air-conditioning and mechanical ventilation in buildings
- NEA — Code of practice for control of Legionella bacteria in cooling tower
- ANSI/ASHRAE/IES Standard 90.1 — Energy standard for buildings