Elevator (Lift)
Among many important functional decisions which must be taken by the designer of a multi-storey building, probably none is more than or as important as the proper selection of the mechanised transportation systems, which include escalators, elevators/lifts, and moving walkways. Not only
are these systems critical to the users, the quality of these systems also affects the tenant’s choice of space against competing buildings. Rising construction costs and the persistent demand for quality space increases the value of designing a mechanised transportation system to deliver the most effective way of moving traffic within the building. For maximum serviceability and economy, mechanised transportation must be planned to meet the requirements of each building and its users.
An elevator or a lift (hereafter referred to as “lift”) is defined as a permanent lifting equipment serving two or more landing levels, including a car for the transportation of passengers and/or other loads, running at least partially between rigid guide rails, either vertical or inclined to the vertical by less than 15°.
The figure below shows examples of the typical installation of a lift without a machine room (machine room-less [MRL]) and a lift with a machine room.
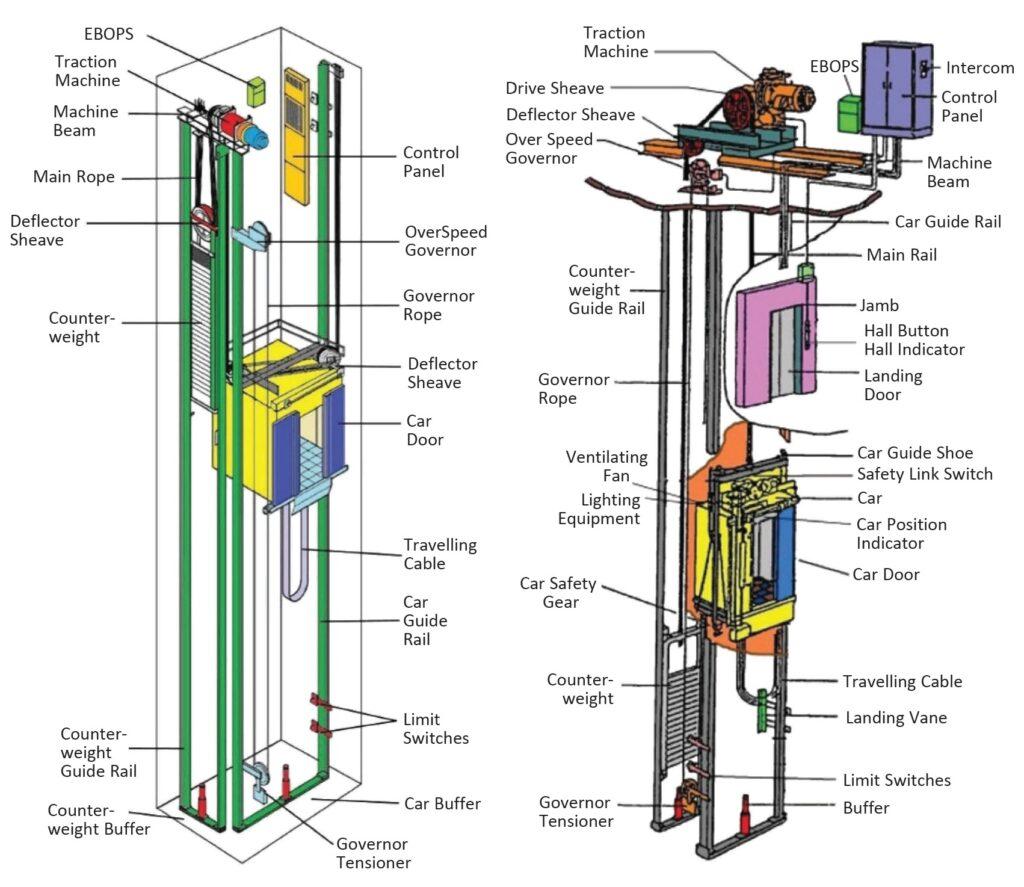
The working mechanism of a lift can either be based on hydraulic or traction:
(1) Hydraulic: Usually found in buildings with 5 or fewer floors. It has a cylinder located in the basement, which is attached to the bottom of the lift. It uses an electrically driven pump to force oil into a cylinder, thereby extending the piston and raising the cab. When hydraulic oil is diverted to a bypass, the lift will seek downward travel.
(2) Traction: Usually found in buildings with more than 5 floors. It has an electric motor to drive a pulley on which hoist steel cables have been installed and attached to the top of the lift car to move it up and down.
The movement of the cars of both hydraulic and traction lifts is controlled by an array of sensors and a computer system. Functional performance tests during installation, depending on local legislative requirements, may include:
- Landing fixture
- Car doors and landing doors
- Safety devices for each door
- Lift car
- Control station in the car
- Car door operation
- Safety gear and over-speed governor
- Automatic control system
- Lift well and pit
- Counterweight
- Hydraulic system (for hydraulic lifts)
For a vertical transport to be deemed effective, it needs to meet the building’s use/purpose. Certain facilities require speed, while others may prioritise stability or comfort. Therefore, the speed of travel and handling capacity may be the top criteria for commercial buildings, while stability for hospital/laboratories, and comfort for hotels.
Accidents associated with lifts are high globally and many cases leading to fatal and permanent injuries have been reported. Some common problems associated with lifts are shown in the figure below:
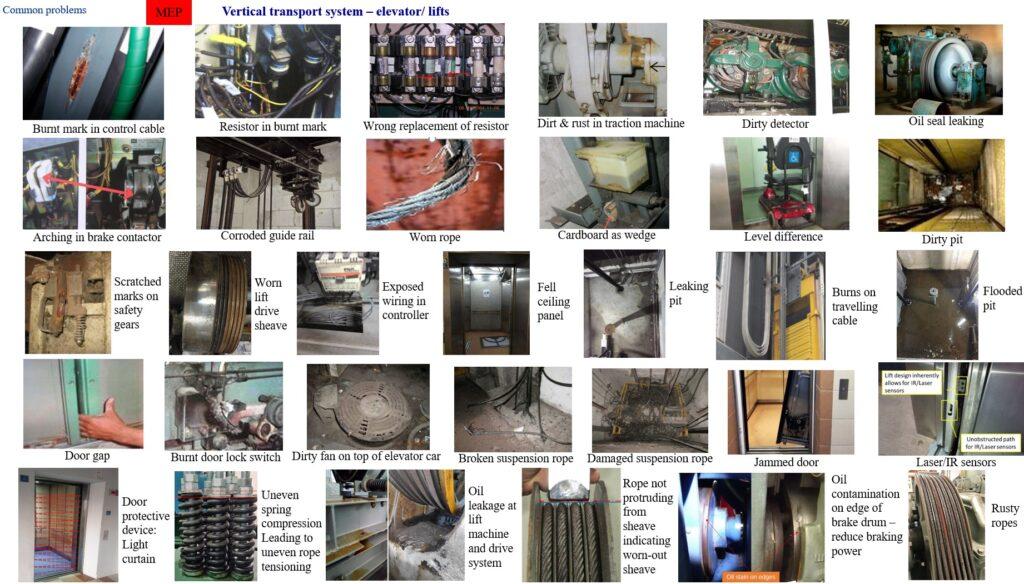
The Building Control Act, Building Maintenance and Strata Management (Lift and Building Maintenance) Regulations, and the respective local regulations, lay out the duties and responsibilities of the building
owner, lift contractor and Approved Person in ensuring the safe operation of lifts. They also prescribe the inspection and tests to be carried out and the documentation to be submitted to their respective building control authority.
All lift owners are to observe the latest requirements of regulatory regime for lifts, which include:
(1) Monthly — As the maintenance of lifts is highly technical, and with the legislative requirements governing it being complex, all lift owners would need to enter into a lift service agreement with a registered lift contractor to maintain their lifts monthly and in accordance with the requirements in the codes and standards. In addition, registered lift contractors will have to maintain lifts according to 20
specific maintenance outcomes, as shown in the table below:
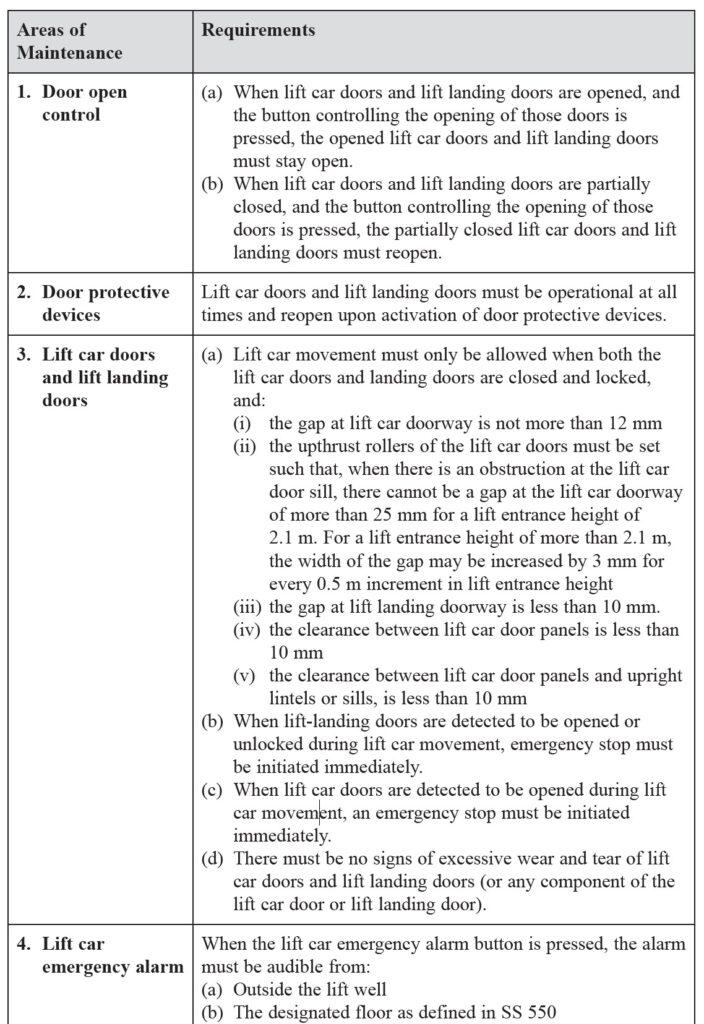
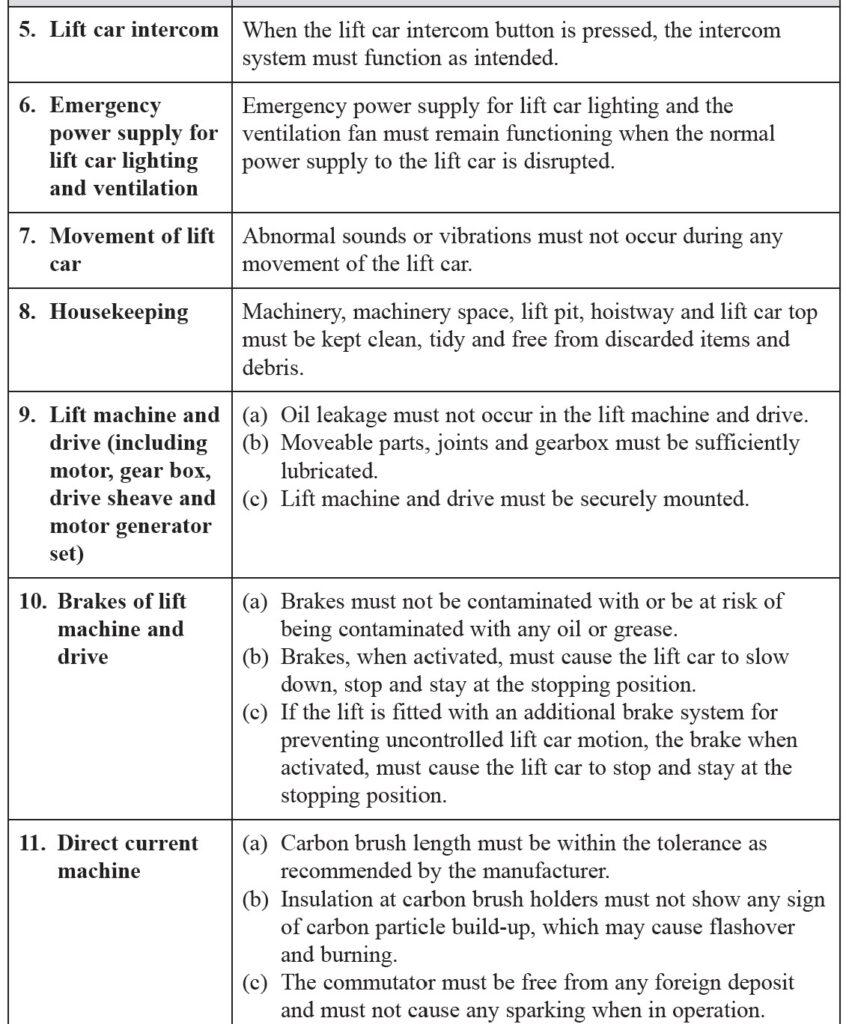
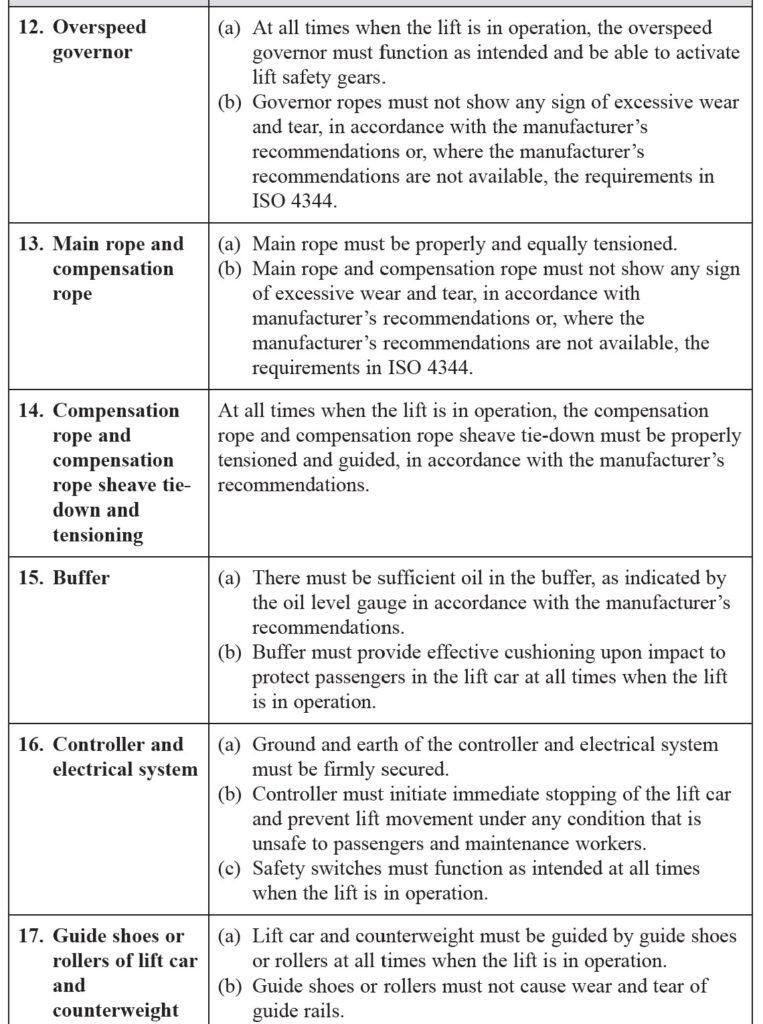
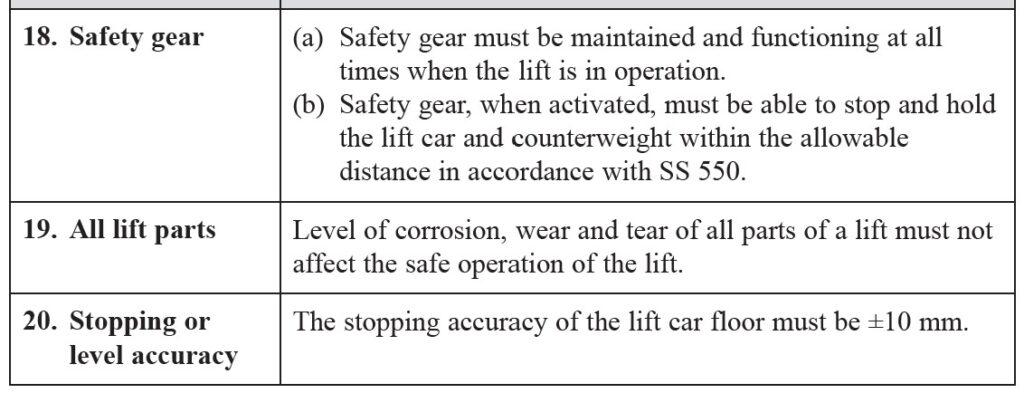
(2) Yearly — The annual examination, inspection and testing of lifts must be carried out by a registered lift contractor in the presence of an independent Authorised Examiner (AE) who is not an associate, partner, director or employee of the lift owner or lift contractor, according to the requirements, codes and standards. This AE is a professional engineer who is registered with the Ministry of Manpower in the competency area of lifts and hoists.
(3) Upon examination, inspection and testing by a registered lift contractor in the presence of an independent AE, the AE will issue a certificate to certify that the lift is in good working condition. The
lift owner will need to apply to BCA for a Permit to Operate (PTO) together with this certificate and other supporting documents for the lift.
(4) Lift owners to display the PTOs in a prominent manner and a conspicuous location in the lifts.
An elevator is a machine that is installed rather than constructed and used for transporting people and things vertically to different levels in a building. Owing to its design requirements, traction elevators demand more maintenance time compared to all other vertical transports, while a hydraulic lift is 2–4 times simpler to maintain; however, its use is restricted to only eight floors. There is no straight forward rule to planning for the most efficient elevator. The service has to be designed in minimum practical time and the equipment should engage a minimum of building’s space. The maintenance scope for elevators may involve lubrication, cleaning, checking, setting, adjustment, repair or changing or parts, and passenger rescue operations under normal circumstances. The process of designing elevator in a building necessitates thorough decisions in making assumptions of total population expected to occupy the upper floors and their traffic patterns, the appropriate calculation of the passenger elevator system performance, and a value judgment of the results so as to recommend the most cost-effective solution.The identified defects pertain to (a) general travel performance and hazards (e.g. elevator machine room condition, elevator pit and lift lobbies); (b) common faults such as elevator car landing gaps and faulty door operation; (c) safety and reliability issues, faulty suspension ropes due to overloading, and failure to activate overspeed governor; (d) energy efficiency and lighting concerns; (e) general requirement for escalators and passenger conveyors. Considerations for maintainability when designing the vertical transport system could ensure its optimal required performance while simultaneously minimising costs for maintenance and operations throughout the building’s life cycle.
Maintainability of the Mechanised Transportation System
A mechanised transportation system is one of the most sophisticated and specialised systems in a facility, with an assembly of mechanical, electrical and hydraulics subsystems distributed from the basement to the roof. Although modern vertical transportation systems are designed and manufactured under tight quality control, once in service, like any other electro-mechanical device, it requires periodic maintenance. A systematic maintenance programme is essential for efficient performance throughout its useful service life whilst balancing customer satisfaction, corporate profit and environmental friendliness. It is important to bear in mind the importance for maintainability when designing the system, since the mechanised transport system is an essential building service for most high-rise buildings and is often difficult to replace.
The mechanised transport systems characteristically have a relatively long service life of 15–30 years. Therefore, it is important for designers and building owners to ensure that the design and quality of the product enable continuous and easy maintenance activities for safety and continued performance, and cleanliness, as well as an aesthetically pleasing appearance.
There is a need to identify shortcomings in a system’s design or a material’s function before it is placed into use, as it is crucial to construct a system component that is maintainable and that functions as it is intended to. Such a practice will be able to sustain its optimum desired performance while, at the same time, minimising maintenance and operation costs during the life cycle of building. The degree to which the design of a building embraces maintenance considerations has a major impact on its performance.
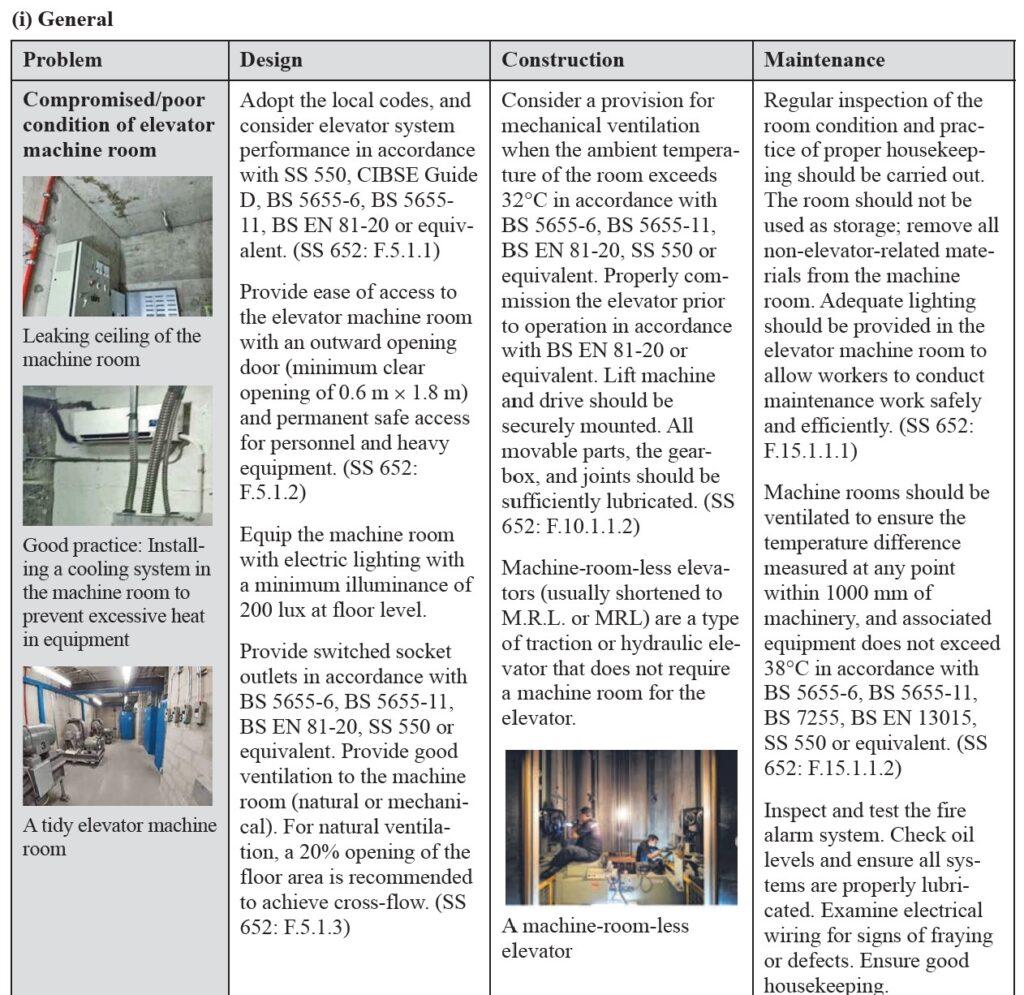
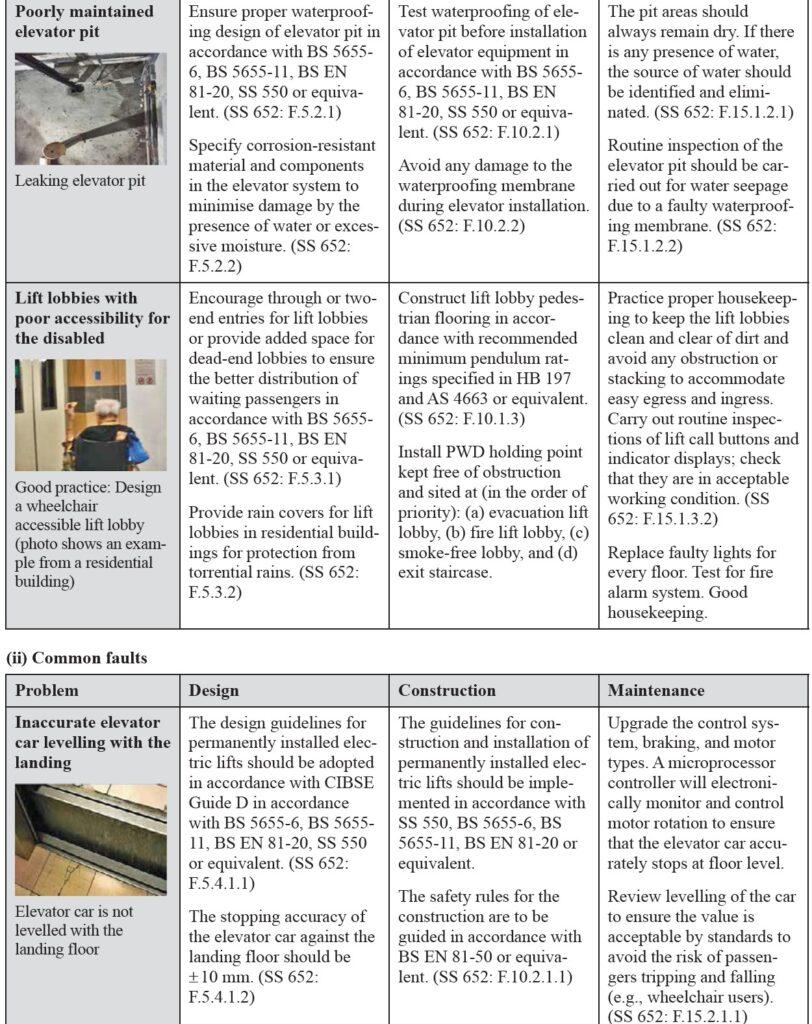
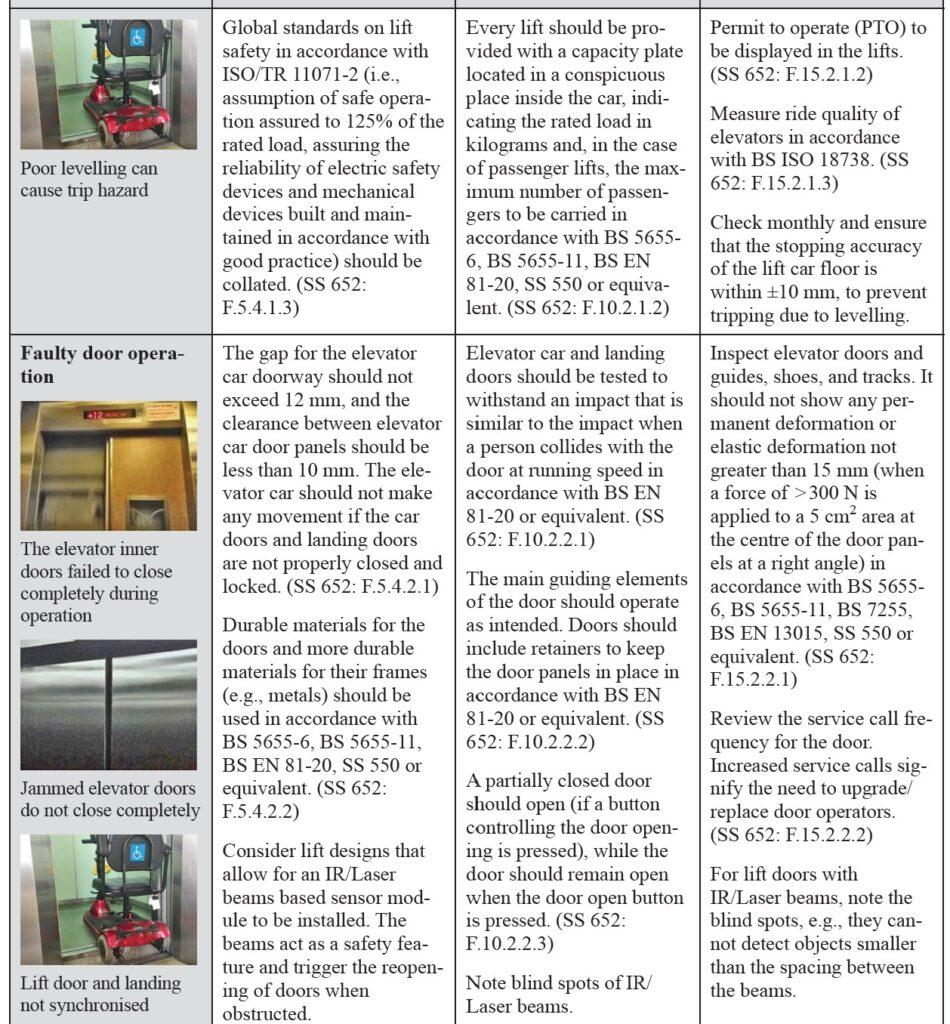
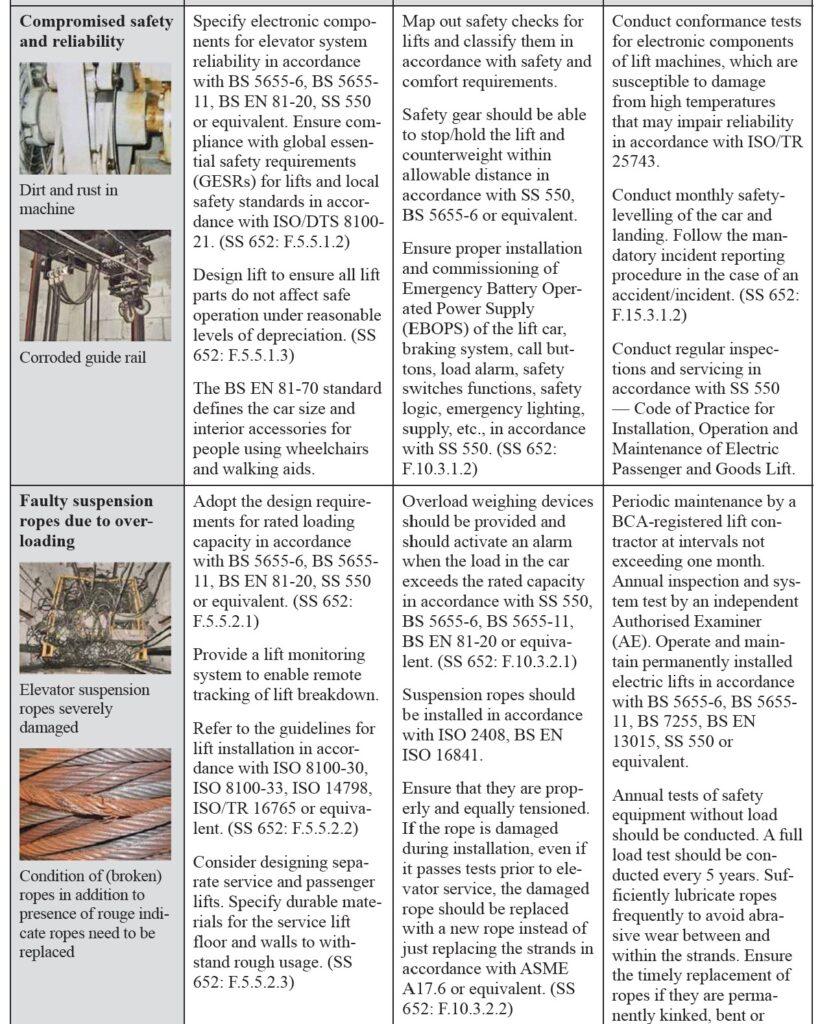
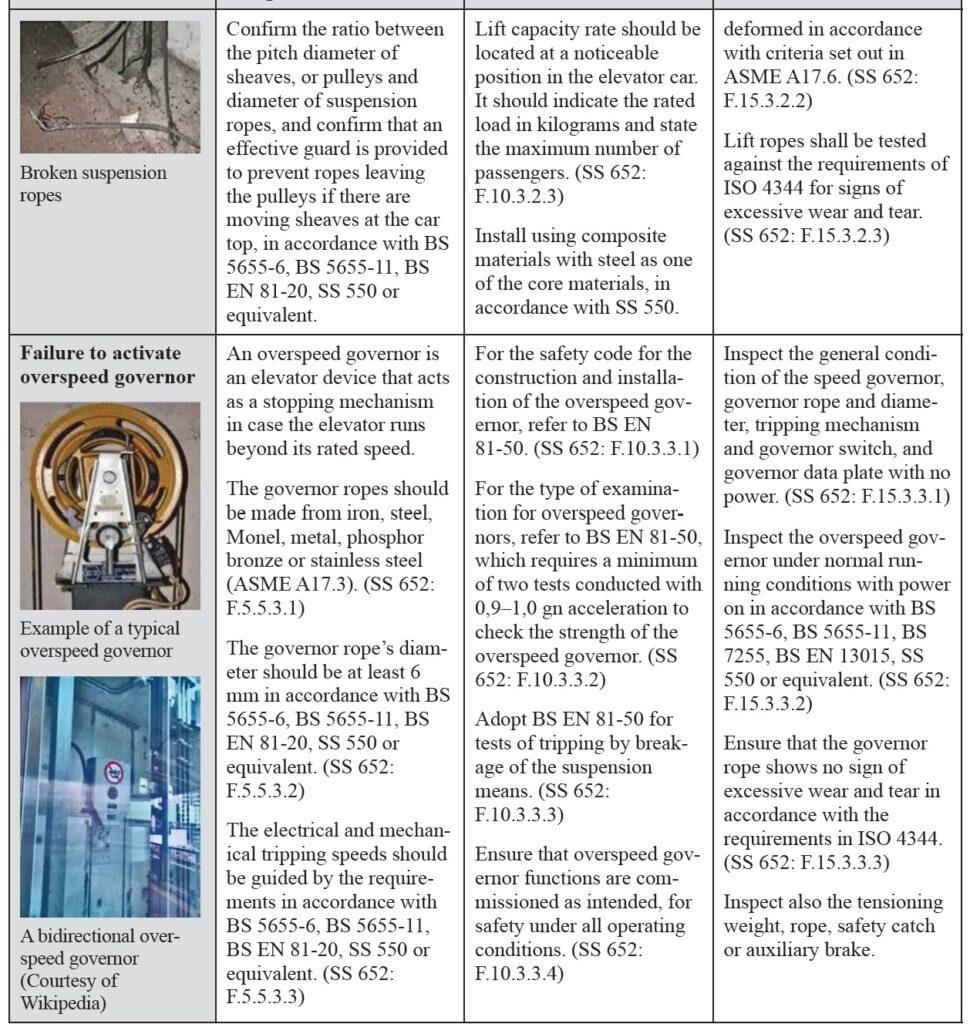
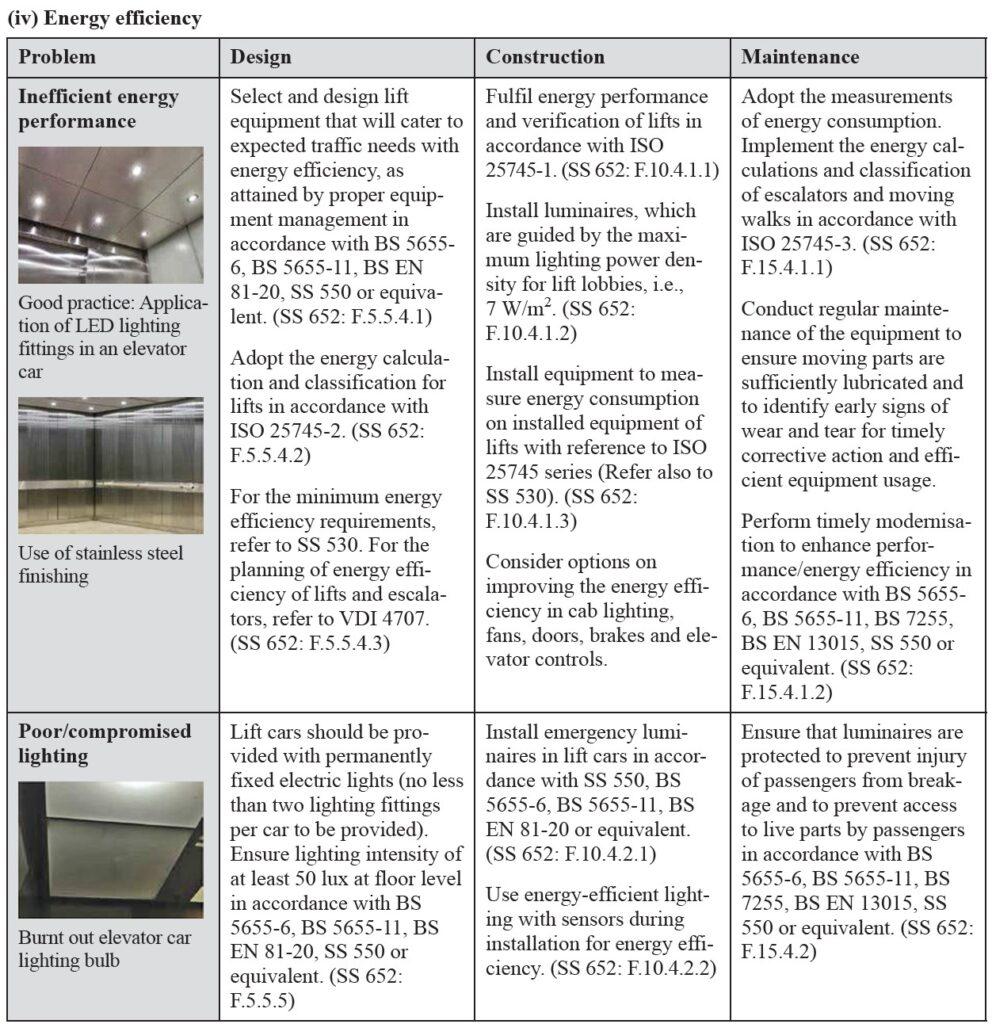
Lift Maintenance Outcome Guidebook – Courtesy of BCA
Reference is made to:
- SS 550 — Code of practice for installation, operation and maintenance
of electric passenger and goods lifts - BS EN 81 — Safety rules for the construction and installation of lifts.
Lifts for the transport of persons and goods - ISO/TR 11071 — Comparison of worldwide lift safety standards
- ISO 8100-20 — Lifts for the transport of persons and goods — Part 20:
Global essential safety requirements - Building maintenance and strata management (lift and building maintenance)
regulations - AS 1735 — Lifts, escalators and moving walks
- JIS A 4302 — Inspection standard of elevator, escalator and dumbwaiter
- ASTM A17.1 — Safety code for elevators and escalators
- ASTM A17.2 — Guide for inspection of elevators, escalators, and
moving walks