Case 2
- Introduction
- Causes of Defects
- Good Practices
- Standards
- Maintenance and Diagnostics
- Remedial
- Similar Cases
- References
Good Practices
Design
Minimise the provision of structural or construction joints to maintain monolithic construction in accordance with BS EN 1992-3 or equivalent. Provide special reinforcement detailing at the joints and 1500 mm lapping. Fibreglass mesh at the joint is also recommended in accordance with BS 6093, BS EN 1992-1-1 or equivalent. Specify compatible membrane that effectively accommodates for movement in accordance with BS 8102 and SS 637 or equivalent.
Construction
Check substrate readiness prior to installation and dampen surface to receive cementitious membrane in
accordance with SS 637 or equivalent. Mix the correct proportions of the waterproofing product until it is homogeneous and lump free. Lay a protective slurry coat above the membrane and cover any openings to protect from debris. Lay protective screed with sufficient fall in accordance with BS 8204-2, BS 8000-0, BS 8000-9 or equivalent.
Waterproofing
Design
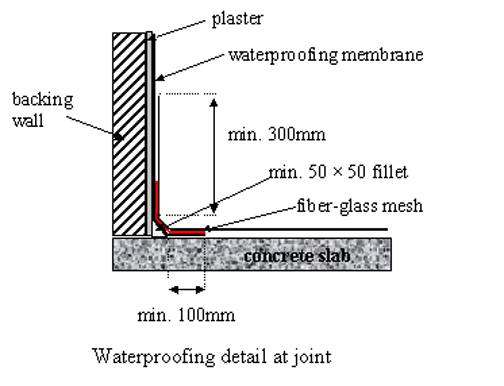
The waterproofing membrane should cover up to a minimum height of 300mm of the wall as shown in Figure 1 to maximize water-tightness of the joint [1-2]. Fiberglass mesh and a fillet should be used to accommodate the relative movement of joint to minimize the risk of damaging the waterproofing membrane. Subsequently, this could enhance the water-tightness of the joints (Figure 1).
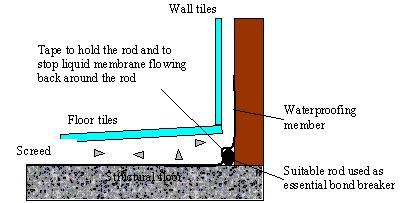
Alternatively, a flexible rod can be used instead of the fibre-glass mesh and fillet as shown in Figure 2.
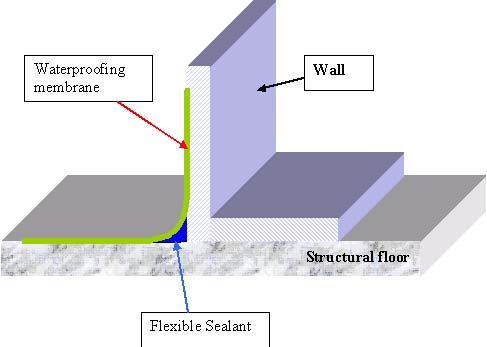
A flexible sealant would also serve the same purpose as the bond breaker (Figure 3).
Material
The decision to select a specific waterproofing system should take into consideration the design of the substrate structure and area of coverage. Due to wet area’s inherent nature of being small with many penetrations, protrusions and discontinuities, a flexible system is more suitable for internal wet areas.
In general, the selected waterproofing material should possess the following qualities:
- Suitable to its micro-environment conditions such as ventilation and surface dampness (Table 1)
- Compatible with the other subcomponents such as screed, tile bedding or even type of tiles (in a vertical surface) (Table 1)
- Easy to apply, especially at pipe penetration areas
- Be elastic and able to bridge over cold joints and differing materials
- Have good adhesion and cohesion strengths
- Able to retain its adhesion and remain stable under extreme fluctuations of temperature
- Able to resist mechanical damage such as peeling, cracking and rupture prior to screed finish
- Fully bonded to the substrate so that any leakage may be localized
Conditions | Justification |
1. Ventilation | Adequate ventilation is necessary for some systems to be cured adequately.
|
2. Surface finish (vertical) | System should be able to accommodate (wall) finishes
|
3. Surface dampness |
Therefore, in general, solvent based systems are not suitable while water based systems are suitable for damp surface conditions. |
4. Construction time | Systems that require long curing time is not suitable for limited construction time:
|
Table 1: Characteristics of a waterproofing system
Waterproofing systems selected for use are required to be specified to relevant local building requirements or to International performance standards. These may include subjecting the materials to stringent tests to determine their performance under actual site conditions.
Construction
The waterproofing membrane should be laid appropriately to ensure the water tightness of the system.
Substrate preparation for application is very important in this process to obtain excellence water-tightness. The following good practices can be carried out:
Surface of the concrete slab should be checked for surface defects after casting. These defects should be removed and repaired to achieve the flatness for waterproofing. This is to ensure excellent bonding between the substrate surface and membrane [17]. | |||||
When the surface has imperfections like honeycombs and defective concrete, it should be repaired or removed down to sound concrete and patched up with suitable mortar such as shrinkage compensated grout, polymer-modified mortar, epoxy mortar etc.
If the surface contains any greasy or oily contaminants, both chemical and mechanical cleaning can be used to remove them. | |||||
![]() | ![]() | ||||
Finally, surface should be cleaned to remove debris and dirt. Some cleaning methods include high-pressure water jet, cleaning with vacuum cleaner or with brooms. | |||||
![]() | ![]() | ![]() | |||
Excess water should be removed to provide dry surface for waterproofing application. Blowers can be used to dry the surface faster. | |||||
![]() | ![]() | ||||
![]() | ![]() | ||||
Fillet is constructed along the joint as a bond breaker at discontinuities such as joints to accommodate the relative movement of abutting elements. | |||||
![]()
Finally, the application of membrane should begin at a corner: diagonal to the entrance, and upturns at wall floor junctions, to avoid stepping on applied area. To minimise water leakages in wet areas, it is a good practice to cover the entire floor area with waterproofing membrane. | |||||
![]() | ![]() | ||||
In the process of application, rollers or brushes can be used in most of the locations. Use of rollers with the same width as the upturn provides an even and uniform application. However, critical locations such as pipe penetrations and joints, could be applied using a brush to ensure good coverage. | |||||
A fiberglass mesh should be used at joints to accommodate the relative movement of abutting joint and to minimize the risk of tearing the waterproofing membrane. |
Quality Control
- Substrates should be inspected and prepared in accordance to the manufacturer’s recommendations prior to the execution of the waterproofing system.
- Waterproofing products should be sealed and delivered in original packaging. All materials should be protected from the weather and stored in a dry and secure place.
- Greater supervision during construction and a skilled labour force are important so as to control and improve the workmanship quality of a product.
- Checklists for the inspection of waterproofing work can be used as means to inspect the onsite workmanship quality. A continual check should be made on the amount of material that has been used and the area covered to ensure that the recommended coverage rate is being achieved.
- The membrane should be tested for water-tightness after completion of the application. Make sure the membrane has cured properly before carrying on the test (Table 2).
System | Time |
Rubber-based systems | 1-72 hrs |
Acrylic-based systems | 48 hrs for total system |
Polyurethane systems | 24-72 hrs |
Cementitious systems | 1-2 hrs and flood test within 24 hrs |
Table 2: Curing Time