Case 4
- Introduction
- Causes of Defects
- Good Practices
- Standards
- Maintenance and Diagnostics
- Remedial
- Similar Cases
- References
Good Practices
Design
Minimise the provision of structural or construction joints to maintain monolithic construction in accordance with BS EN 1992-3 or equivalent. Provide special reinforcement detailing at the joints and 1500 mm lapping. Fibreglass mesh at the joint is also recommended in accordance with BS 6093, BS EN 1992-1-1 or equivalent. Specify compatible membrane that effectively accommodates for movement in accordance with BS 8102 and SS 637 or equivalent.
Construction
Check substrate readiness prior to installation and dampen surface to receive cementitious membrane in
accordance with SS 637 or equivalent. Mix the correct proportions of the waterproofing product until it is homogeneous and lump free. Lay a protective slurry coat above the membrane and cover any openings to protect from debris. Lay protective screed with sufficient fall in accordance with BS 8204-2, BS 8000-0, BS 8000-9 or equivalent.
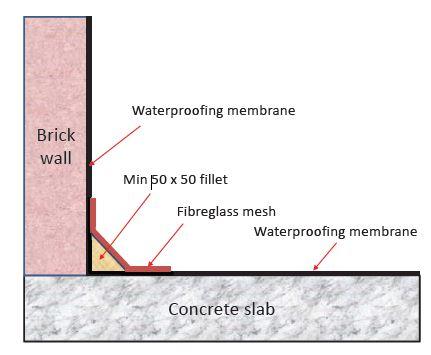
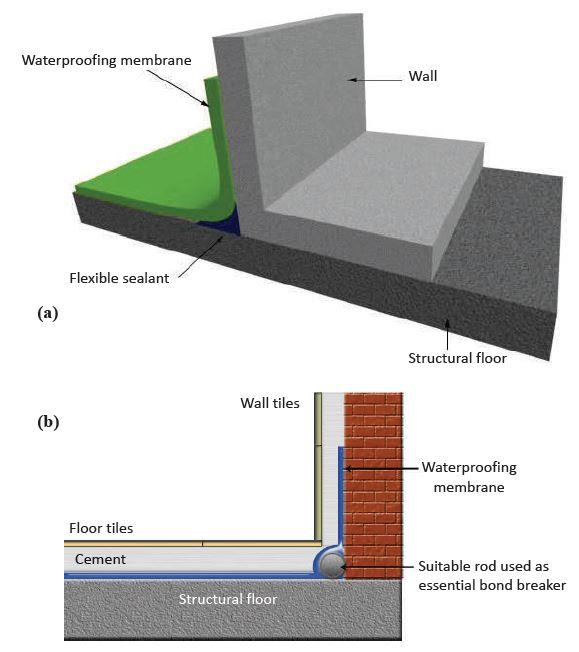
Wall
Design
- Wall thickness and wall finishes should be designed to achieve the proper water tightness under the exposed conditions [2].
- Ensure that detailing allows for movement joints that are applied with flexible/ elastomeric weather seal to accommodate movement between materials due to differential coefficient of expansion [3].
- Use steel mesh to prevent cracks at junctions of brickwall and other materials.
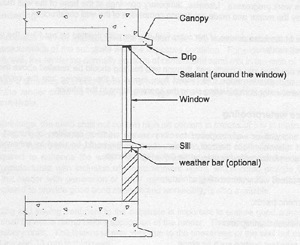
- A canopy to throw water off the face of the external wall and sill to prevent water seepage through windows is an important detail in the facade (Figure 1). In addition, the window can be recessed into the façade to keep away from wind-driven rain. This reduces the incidences of water penetration through the window.
- The joints between window and the wall should be watertight. Drainage systems such as weep holes can be designed to improve the water-tightness [4]. Figure 2 shows typical examples of weep holes.
- In addition, proper drainage system should be provided to drain off the rain water away from the external wall.
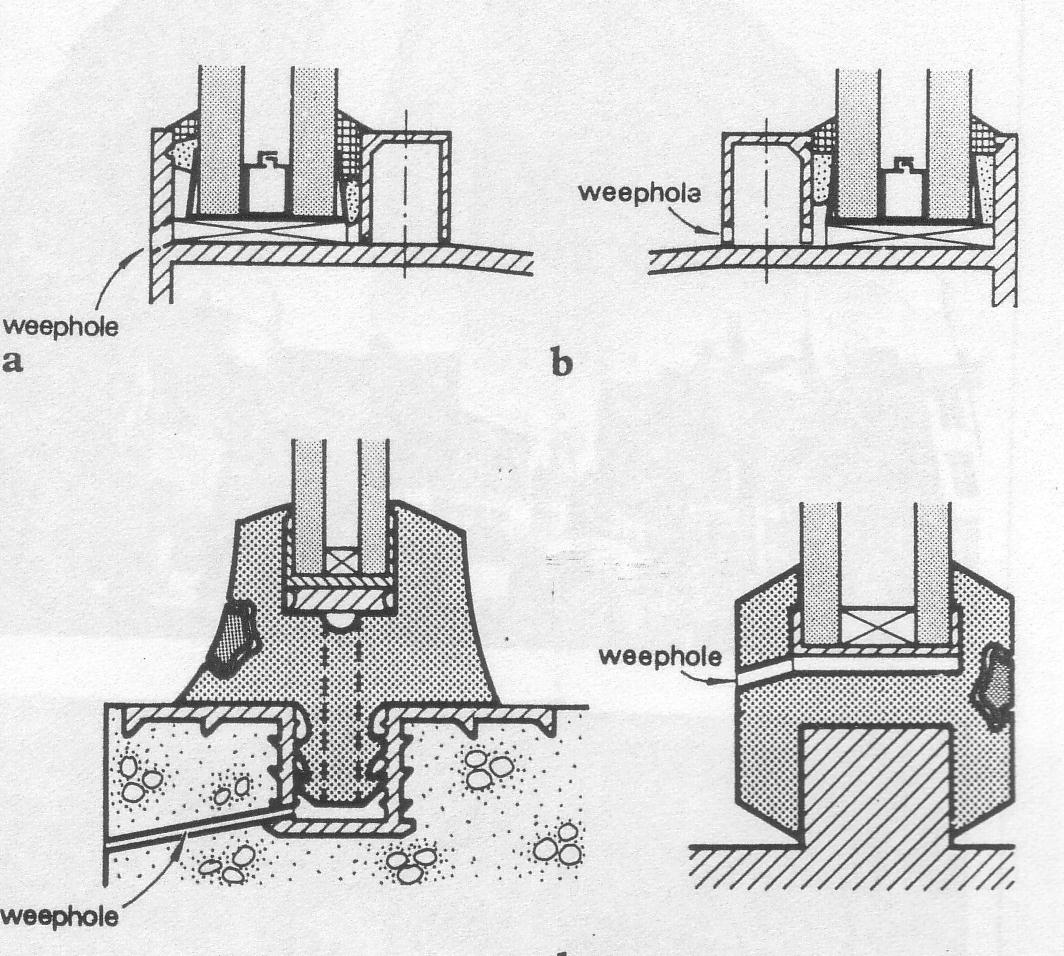
Construction (Brickwork)
- In laying the bricks, good workmanship is required to lay the bricks.
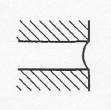
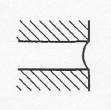
- Mortar joints should be cast in place properly to enhance watertightness. Mortar joint finishes should be weathered and concave if they are exposed (Figures 3a & 3b).
- Ensure that the mortar mix is of the right cement: water ratio to prevent cracking. The mix for the coat should not be stronger than the background. Problems of inaccurate site batching and misuse of additives can be reduced by specifying premixed material.
- If the face of the facade is frequently subjected to rain and moist conditions, it is recommended to apply a layer of clear water-repellant on the bricks to prevent water penetration.
Quality Control
- Brick units should be thoroughly wetted before laying to reduce the absorption of water from mortar thus, reduce the risk of mortar cracking.
- A suitable cement mortar mix should be used to minimise the water penetration through mortar joints. The cement mortar should possess the desired characteristics of high water retentivity, high plasticity, good adhesion and should not shrink excessively during and after hardening [3].
- Admixtures for mortar are generally not recommended because of their unknown ingredients and the lack of data on their effect on bond strength and, consequently, watertightness of masonry walls.
Plaster
Material
- Specify rendering mixes appropriate to the exposure conditions and according to the strength of background wall or of earlier coats: coats should be richer than the preceding coat or stronger than the background (Table 1) [5].
Background | First coat | Second coat | Final coat | |||
Mix | Thickness (mm) | Mix | Thickness (mm) | Mix | Thickness (mm) | |
Strong to moderate | 1:3 to 4 or approved pre-mixed mortar | 8 – 12 | 1:3 to 4 or approved pre-mixed mortar | 6 – 10 | 1:3 to 4 or approved pre-mixed mortar | The final coat should be applied as thin as possible. However, it is largely determined by the size of coarse particles in the sand. For e.g. with sands up to 3mm, the final coat can usually be finished about 6mm. |
Metal lathing | 1:3 or approved pre-mixed mortar | 3 – 6 | 1:3 or approved pre-mixed mortar | 10 – 14 | 1:3 or approved pre-mixed mortar | |
Moderate to weak | 1:5 to 6 or approved pre-mixed mortar | 8 – 12 | 1:5 to 6 or approved pre-mixed mortar | 6 – 10 | 1:5 to 6 or approved pre-mixed mortar | |
Note: The nominal overall thickness (excluding texture) should not normally be less than 20mm.
The nominal overall thickness (excluding texture) should not normally exceed 18mm for RC surfaces |
Table 1: Renders for severe exposure conditions
- A suitable wall finish should be provided to improve the water-tightness of the external wall. E.g. wall rendering consists of cement and sand mix in the ratio of 1:3 to 1:5 [3]. Table 2 shows some recommendations of plaster mix proportions.
Mix | Mix proportions by volume based on damp sand | ||||
Cement: Lime: Sand 1) | Cement: Ready-mixed lime/sand 1) | Cement: sand* (Using plasticizer) | Masonry cement: sand* | ||
Ready-mixed lime: sand | Cement: ready-mixed material | ||||
I | 1 : ¼ : 3 | 1 : 12 | 1 : ¼ : 3 | – | – |
II | 1 : ½ : 4 to 4 ½ | 1 : 12 | 1 : ½ : 4 to 4 ½ | 1 : 3 to 4 | 1 : 2 ½ to 3 ½ |
III | 1 : 1 : 5 to 6 | 1 : 12 | 1 : 1 : 5 to 6 | 1 : 5 to 6 | 1 : 4 to 5 |
IV | 1 : 2 : 8 to 9 | 1 : 12 | 1 : 2 : 8 to 9 | 1 : 7 to 8 | 1 : 5 ½ to 6 ½ |
V | 1 : 3 : 10 to 12 | 1 : 12 | 1 : 3 : 10 to 12 | – | – |
*With fine or poorly graded sands, a lower volume of sand should be used.
Table 2: Wall finishes
Note: In special circumstances, e.g. where soluble salts in the background are likely to cause problems, mixes based on sulphate-resisting Portland cement should be employed.
- Expansion joints in the form of grooves should be provided and plastering should not be done to walls with large surface areas. Gable walls or other walls that are exposed to sunlight are most prone to drying shrinkage.
- The waterproofing coatings can be used for fair-faced brick wall or walls exposed to more severe weather condition or subjected to frequent impingement of rainwater from the roof as [6-7]:
- Plaster mixed with waterproofing admixtures
- Elastomeric paints
- Cementitious coating
- Water-repellent coating such as silane
Many coating and membranes are available in the market to protect the surface from moisture seepage. In recent years, it has been developed a new class of materials called silicones, which have come into use in the building field mainly with attempts to correct problems of penetration of rain into unit masonry. Some manufacturers also advocate their use for the prevention of efflorescence on masonry walls. When a brick or some other type of unit is treated with silicone, its surface usually becomes highly water-repellent.
Ventilation
Design
- Adequate ventilation should be provided to enhance the drying process and reduce dampness inside the wet area [8].
- Proper air circulation can be designed by natural, mechanical or a combination of both mechanical and natural ventilation systems. In public toilets, the mechanical systems of exhaust fans and ventilation ducts should be located within 3m of the fan inlet or intake grill [9].