Case 1
- Introduction
- Causes of Defects
- Good Practices
- Standards
- Maintenance and Diagnostics
- Remedial
- Similar Cases
- References
Good Practices
Concrete
Construction

Figure 1
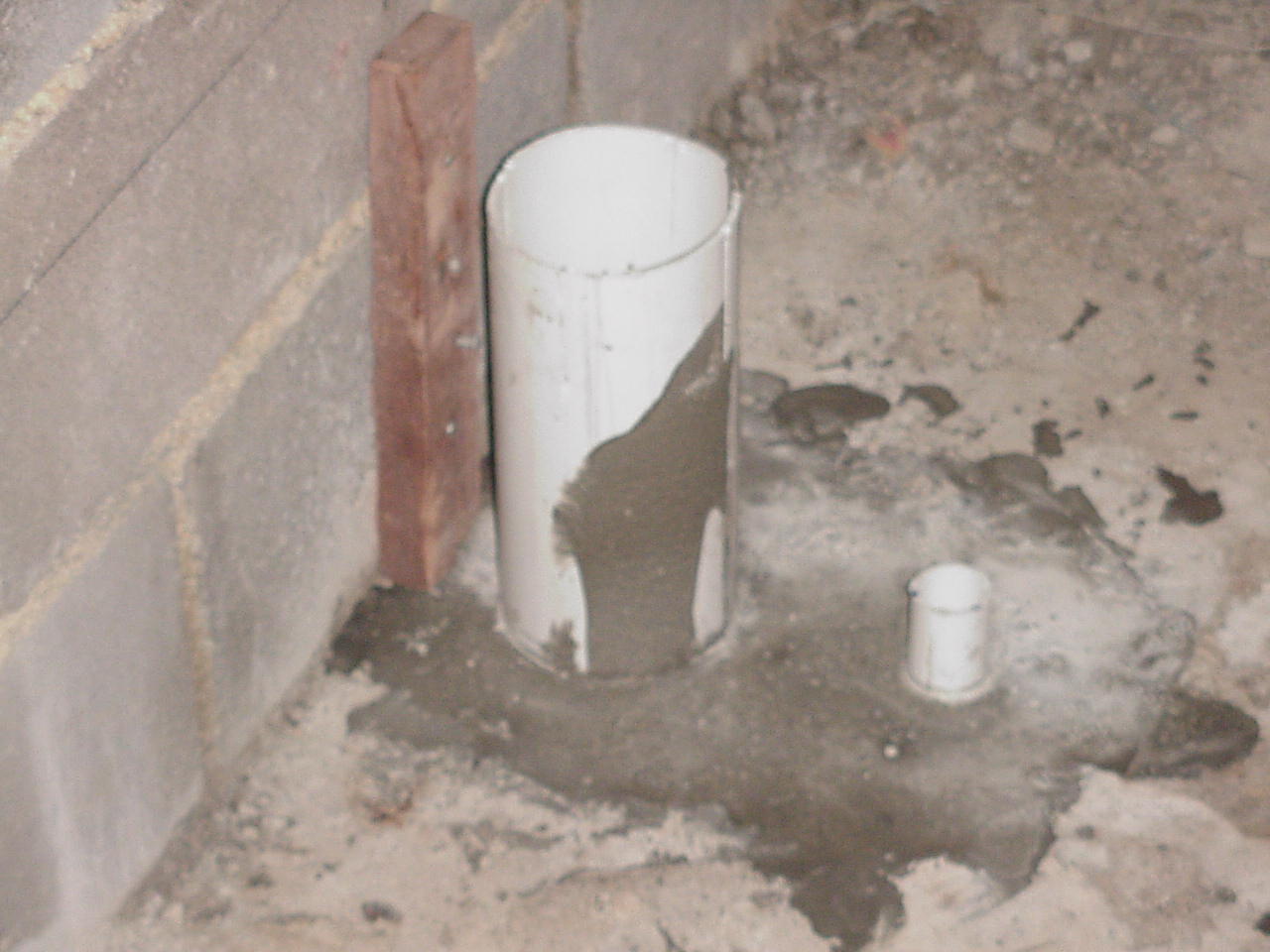
Figure 2
- Pipes and pipe sleeves should be cast with the floor slab (Figure 1) rather than leaving openings or hacking after concrete has cured (Figure 2) and to minimize water leakage caused by the porous concrete around it.
Waterproofing
Design
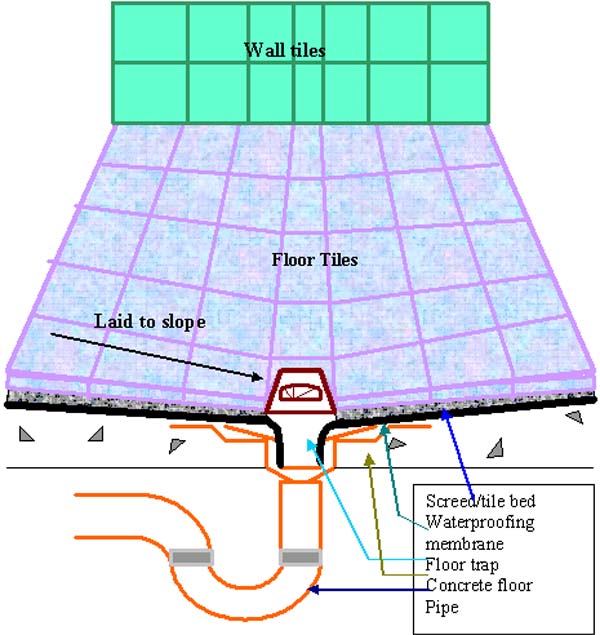
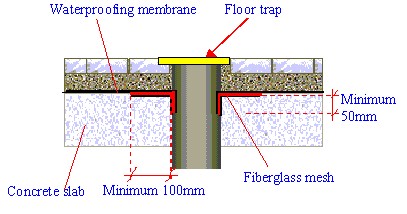
- Proper design details of waterproofing membrane at floor traps should be provided as below (Figure 3a & b) [1-2].
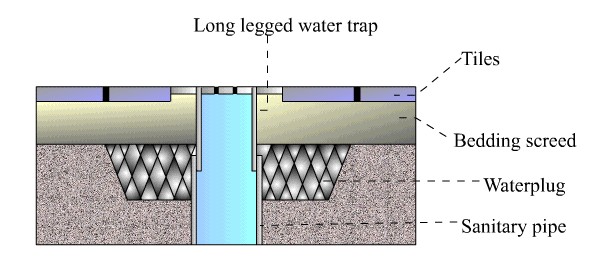
- Water plug can be cast around the pipe (Figure 4). This water plug would work synergistically with the waterproofing material to provide water tightness around the penetrations.
Material
A suitable waterproofing system should be selected based on lifetime performance of the system.
In general, the selected waterproofing material should possess the following qualities:
- Suitable to its micro-environment conditions such as ventilation and surface dampness
- Compatible with the other subcomponents such as screed, tile bedding or even type of tiles (in a vertical surface)
- Easy to apply, especially at pipe penetration areas
- Be elastic and able to bridge over cold joints and differing materials
- Have good adhesion and cohesion strengths
- Able to retain its adhesion and remain stable under extreme fluctuations of temperature
- Able to resist mechanical damage such as peeling, cracking and rupture prior to screed finish
- Fully bonded to the substrate so that any leakage may be localised
Check the performance of waterproofing membranes before selecting a suitable system.
Construction
Flowing application should be followed up to obtain monolithic structure at the floor trap [6-7].
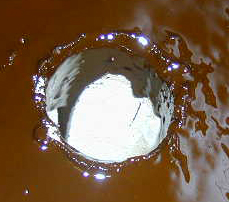
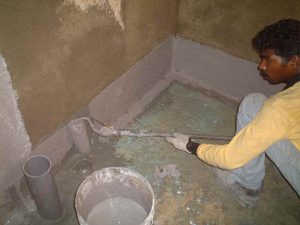
Care must be taken to ensure required coverage around floor traps (Figure 5). Brush application of membrane is more suitable at floor trap to ensure good coverage (Figure 6)
Before application process begins, the substrate receiving the waterproofing membrane should be checked and prepared for better bonding as follows:
![]() ![]() ![]()
Surface should be prepared for membrane application by cleaning with water. The use of chemical or mechanical cleaning methods depend on the level of contamination or amount of dirt on the surface (Figure 7a, b & c) | |||||
![]() ![]()
Excess water should be removed to prepare dry surface for waterproofing (Figure 8a). Mechanical blowers can be used for faster drying (Figure 8a, b). | |||||
![]() |
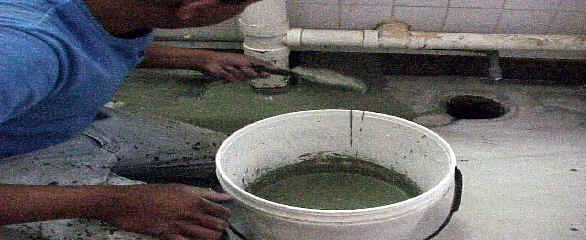
- Apply material onto prepared surface by brush, roller, serrated trowel, spray or a combination of these methods, as specified by the manufacturer. However, brush application of membrane is more suitable at floor trap to ensure good coverage (Figure 10).
- Waterproofing membrane should be applied into the floor trap to minimum downturn of 100mm.
Quality Control
- Substrates should be inspected and prepared in accordance to the manufacturer’s recommendations prior to the execution of the waterproofing system.
- Waterproofing products should be sealed and delivered in original packaging. All materials should be protected from the weather and stored in a dry and secure place.
- Greater supervision during construction and a skilled labour force are important so as to control and improve the workmanship quality of a product.
- Checklists for the inspection of waterproofing work can be used as means to inspect the onsite workmanship quality. A continual check should be made on the amount of material that has been used and the area covered to ensure that the recommended coverage rate is being achieved.
- The membrane should be tested for water-tightness after completion of the application. Make sure the membrane has cured properly before carrying on the test (Table 1).
System | Time |
Rubber-based systems | 1-72 hrs |
Acrylic-based systems | 48 hrs for total system |
Polyurethane systems | 24-72 hrs |
Cementitious systems | 1-2 hrs and flood test within 24 hrs |
Table 1: Curing Time
Plumbing
Design

It is a good practice to have minimal number of penetrations (Table 2) to minimize the inhomogeneity of the waterproofing membrane. Designing a common stack, the number of penetrations can be minimized (Figure 11) [4-6].
Fittings | Recommended number of penetrations |
Urinal/WC | 1 trap shall be provided to serve a maximum of 10 urinals. For more than 10 urinals, more than one trap shall be provided. |
Washbasin | 1 washbasin trap shall be provided to serve a maximum of 10 washbasins. For more than 10 washbasins, more than one trap shall be provided. |
Wash/shower/bath | 1 floor trap for every 3 WC cubicles provided that the separating wall/ partition does not touch the floor level and the other 2 WC cubicles are graded to fall towards the floor trap (FT) in the third WC cubicle. |
Table 2: Recommended number of penetrations for different sanitary fittings
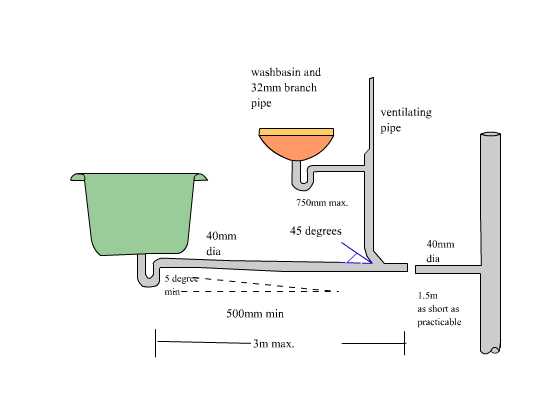
- Adequate gradients and specified lengths should be kept so that they would drain efficiently [4-6] (Figure 12).
Construction
- The floor trap should be properly fixed to achieve water-tightness.
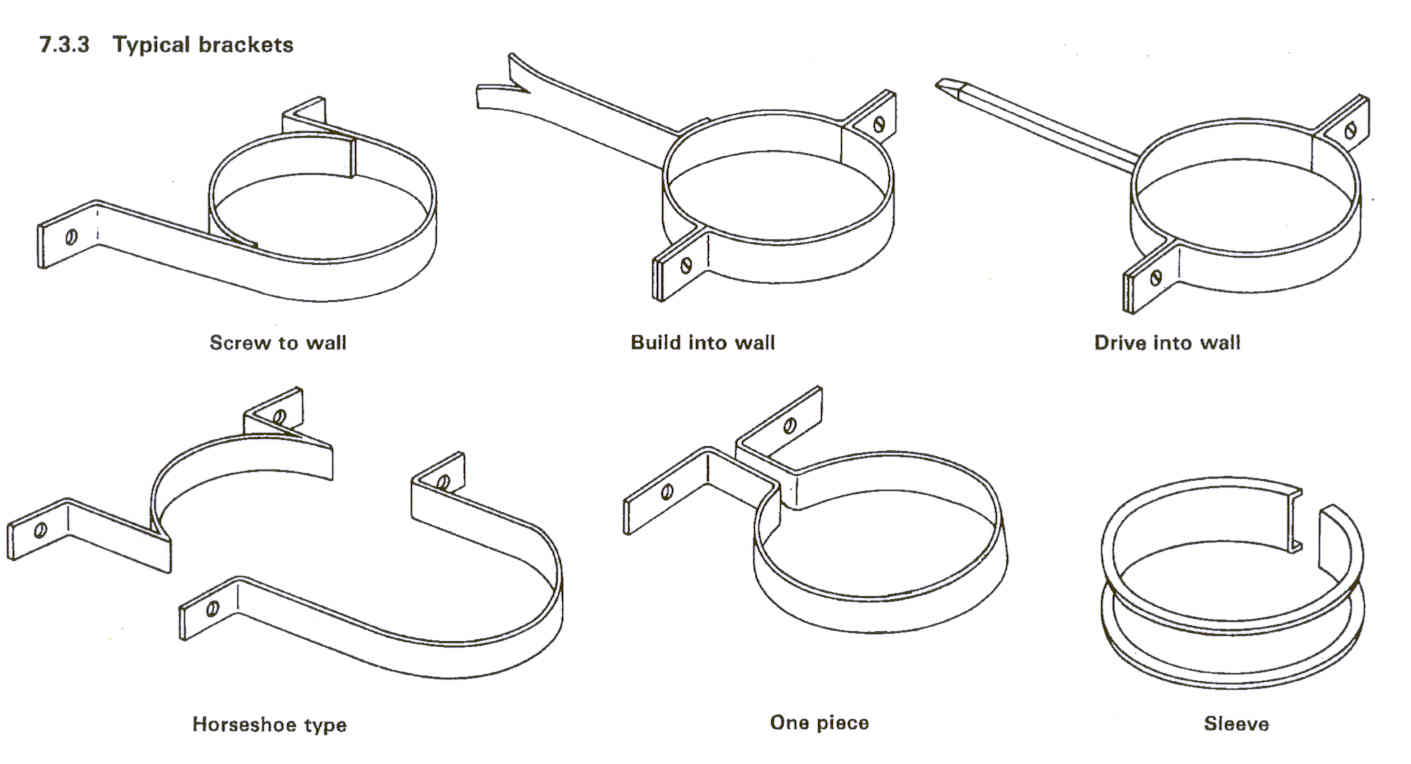
- Fix the pipes according to the relevant allowances for movement (Table 3), providing either sliding supports for locations or rigid fixing for clamping (Figure 13) at intervals given in the Table 3, to minimise the risk of damaging pipes [6].
Maximum distance between sanitary pipe supports | |||
Pipe material | Pipe size (mm) | Vertical pipes (m) | Low gradient pipes (m) |
Plastic pipes | 32 – 405075 – 100150 | 1.21.21.81.8 | 0.50.60.91.2 |
Cast iron | all sizes | 3.0 | 3.0 |
Table 3: Maximum distance between pipe supports
- Remove any burs and swarf and ensure pipe bores are clean before jointing when the pipe is cut.
- Plastic pipes or galvanized pipes should not be bent during installation.