Cathodic Protection
Cathodic Protection is an electrochemical means of corrosion control in which the oxidation reaction in a galvanic cell is concentrated at the anode and suppresses corrosion of the cathode in the same cell [1].
CP reduces corrosion by changing the thermodynamics of the steel, i.e., the chemical potential of the steel in contact with the concrete is changed to make it more inert. This is done by forcing an electrical current at the steel/concrete interface. Most CP systems are impressed current, i.e., the current is impressed by a rectifier and an anode. The anode should cover as much of the surface of the protected concrete structure as possible in order to improve both the distribution of the current to the reinforcement and the service life of the system.
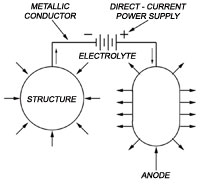
Source: www.odot.state.or.us/…/patterson/ images/cathodic.jpg
The best anode systems developed so far are listed in Table 1 along with recommended applications and comments.
Anode type
|
Application
|
Comments
|
---|---|---|
Conductive coatings, i.e., paint filled with graphite powder | Soffit of parking garages and bridge decks; columns, walls | Can be brush or spray applied. However, it is recommended that the coating of choice have a good track record since some have had very poor performance in the past due to improper formulation. Least expensive systems, but service life is occasionally inferior depending on the coating quality. However, strongly recommended if scaffolding is not extensive or costly. |
Metallized zinc | Bridge-deck soffits, columns. Could be used in parking garages (galvanic) | Good track record on all systems tested. Long service life predicted. Costly as impressed-current anode, but could be used more affordably as galvanic anode when the concrete is relatively moist and the cover is thin, based on present experimental data. |
Table 1. Most frequently used anode systems
Source: http://irc.nrc-cnrc.gc.ca/practice/coa4_E.html
Reference:
[1] http://www.marpo.gr/cathodic_protection/cathodic_protection.html