Fire hydrants are usually pillar like structure, which emerges from below ground level, intended primarily to supply water to hoses for fire fighting. It is supported with breeching inlet, wet or dry riser, and landing valve. The design is based on hydraulic requirement of pressure of the jet and follows the guideline provided by SCDF (2007) & SS CP 29. Compatibility in terms of size or nominal diameter with fire brigade equipment is maintained by all standard manufacturers.
Defects
|
Probable causes for the defect
|
Design for Maintainability (DfM) Guidelines
|
Difficult access / detection
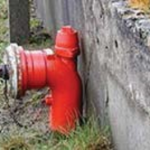 Inaccessible hydrant points due to positioning
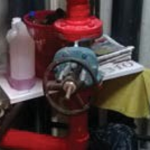 Improper housekeeping practices, and storing of combustible material in wet riser |
- Obstructed by parking, landscaping – poor project coordination.
- Not installed at adequate height as per specification.
- Improper location or positioning
|
Design
- Conform to the location and number of fire hydrants as per Fire Code [8].
- Comply with the positioning of breeching inlets as close as possible to rising main/hydrant (BS 9990:2015, SS 575:2012, NFPA 14:2016).
- Locations should be accessible, with no obstructions from parking, loading bays, landscaping, building elements, etc.
- Provide protection to hydrants from mechanical damage.
- Specify easily visible/ identifiable signage and colour as per SS 508-3:2013 (see also ISO 3864-1:2011).
Construction
- Ensure good project coordination.
- Installation should be secure and safe, with special consideration given for potential sources of damage.
- Ensure connections and position of valves comply with specifications. Risers must be securely anchored before any pressure or flow test is performed.
- Hydrants should be made operable immediately after completion, and should be tested to protect the construction site.
- Mounting height of hydrant and breeching inlet should be strictly maintained during installation (BS 9990:2015, SS 575:2012, NFPA 14:2016).
Maintenance
- Perform proper daily housekeeping practices at hydrant points to remove obstructions (debris, stacked material) that impede accessibility.
- Ensure that the storage tanks are accessible for maintenance. Ensure that the valve pit is accessible for inspection and cleaning.
- Conduct semi-annual check for rust, dirt, or foreign material on valves, or other operating parts; as well as clean, paint and lubricate as required.
- Ensure that additional building elements, landscaping, etc. (during building operation and maintenance phase) do not impede accessibility to hydrant points (BS 9990:2015).
|
Faulty – damaged, leaky, jammed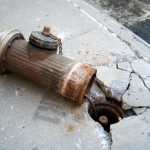
Damaged hydrant
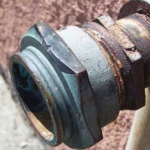 Damaged and unusable breaching valves |
- Damaged by corrosion, physical damage. E.g. knocked by vehicles.
- Parts-stem, cap, plug, thread etc damaged during installation or rusted (if not lubricated or painted).
- Outlet is not properly tightened after testing.
- Missing operating nozzle – careless use, not secured.
|
Design
- Specify hydrant pillar to be constructed of materials that are strong and rust-proof (e.g. gunmetal parts) (BS EN 1982:2008).
- Rising main and other pipework should be made of wrought iron or steel. Pit covers on roadways should be able to withstand vehicular load (BS 9990:2015, SS 575:2012, NFPA 14:2016).
Construction
- Ensure the proper installation of all components (parts-stem, cap, plug, thread, etc.) without damaging them.
- Lubricate and paint for additional protection.
- Tighten outlet properly after commissioning and testing.
Maintenance
- Conduct weekly check of isolating valves to ensure that they are kept locked in open position daily and that breeching inlets are functioning (NFPA 25:2017).
- Conduct monthly checks for any leakage, blockage or corrosion, and for workable line pressure.
- Perform thorough inspection of booster pump and associated systems semi-annually.
- Ensure that a thorough inspection of the hydrants is annually performed by a competent professional.
|
Unacceptable working condition.
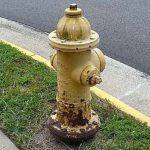
Highly corroded body
|
- Such examples are: dry riser having water or less pressure in wet riser. It happens mainly if valves are faulty or leaky.
|
Design
Construction
Maintenance
|
Rusted riser
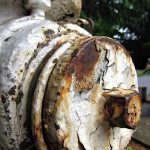
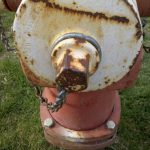
|
- Poor make.
- Cyclic wetting and drying if the tests are conducted carelessly.
- Use of raw / dirty water. Tanks may not be cleaned for long.
|
Design
Construction
Maintenance
|
Jammed inlet
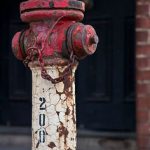
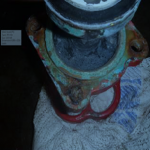
|
- Dirt deposition in the rubber cap or breeching inlet.
|
Design
Construction
Maintenance
|
References
[1]
Normative References/Standards Referred to for Air Handling Unit and Fan Coil Unit