Sprinklers are considered the most effective fire suppression equipment. Buildings fitted with sprinkler seldom suffer from severe fire damage (Fontana et al, 1999). Because of its importance, NFPA 101 Life Safety Code makes use of sprinkler mandatory all of the occupancies.
Sprinkler’s requirement of water to maintain adequate and flow rate are based on hydraulic design. If direct supply from public main is not sufficient, then it is boosted by fire pumps which in tern get its supply from gravity tank, suction reservoir or natural sources like river (SS CP 52).
Defects |
Probable causes for the defect |
Design for Maintainability (DfM) Guidelines |
Faulty/ compromised sprinkler system/ No more functional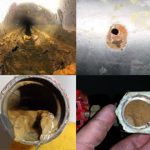
Corroded and faulty sprinkler
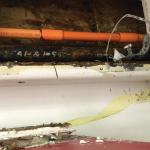 Leaky sprinkler pipe
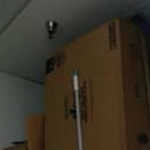 Obstructed sprinkler
|
- Unsuitable choice of type and function of sprinkler makes it non-operative within a short period of time.
- Covered by paint or other foreign material.
- Poor maintenance – dirty, damaged by use of wrong wrench
- Empty gas bulb – needs replacement with time.
- Excessive corrosion and scaling if pipe is not rust resistant.
- No remedial measure taken for initial corrosion and pitting.
- Microbiologically influenced corrosion (MIC) due to use of raw / untreated water, irregular flushing.
- Poor consideration for potential obstructions in planning.
- Obstructed by poor housekeeping – stacking of material.
- Wrong orientation / hindrance by supports (careless installation).
- Replaced with different type (usually if spare unit not in stock), grease / dirt in spray nozzle.
|
Design
- Sprinkler design requirements should consider hydraulic principles and parameters such as, hazard class, discharge density, and AMAO (assumed maximum area of operation) (SS CP 52:2004, ISO 6182 series, NFPA 13:2016). The usual requirement is 75L/min for 2.5m wide area.
- Specify rust resistant material to avoid corrosion, pitting and scaling.
- Potential obstructions should be considered during planning stage.
Construction
- Installation and testing of sprinkler system, its associated controls, fire pumps and water supply should comply with SS CP 52:2004. (See also NFPA 13:2016).
- Mounting should be carried out according to the design approved by the authority and as per manufacturer’s instructions. Conform to general guidelines as per NFPA 13:2016.
- Ensure the careful installation of sprinkler system to maintain correct orientation without hindrance by supports.Maintain spare sprinklers and sprinkler spanner after installation for future needs.
Maintenance
- Conduct quarterly visual inspection of all sprinklers for any leakage, damages or grease/dirt in spray nozzle and replace as necessary.
- Conduct annual inspection of pipes and hangers for corrosion and mechanical damage (clean, paint or replace as necessary).
- Clean quarterly and remove any obstruction affecting efficient discharge from sprinklers. Check for any sign of corrosion or deposit of dirt, paint or foreign material (NFPA 13:2016).
- Practice good housekeeping to avoid stacking of material leading to obstruction of sprinklers.
- Conduct monthly test of smoke detectors and regular maintenance to ensure continuous operation
|
Blocked pipe
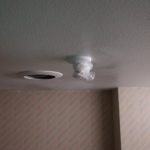

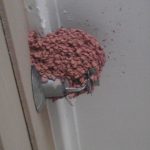
|
- Excessive scale and sedimentation from raw water, inferior material or irregular flashing.
- Misaligned, careless workmanship -tools, loose fittings left inside
|
|
Sagging pipe
Broken pipe brace
|
- Effect of vibration, water flow etc not taken into account in design or mounting location is not enough strong.
- Strength of supports never cross checked during installation.
- Pipe hanger and seismic brace become loose and worn with time.
|
|
Pump- excess vibration, noise overheating |
- No safe working condition or enough space in pump room for regular inspection, maintenance or replacement of pumps.
- Insulating pad not provided to reduce noise and vibration.
- Defects during installation remain unnoticed.
- Pumps are not maintained regularly. E.g. cleaning, lubrication, inspection and testing.
|
|
Leakage in valves
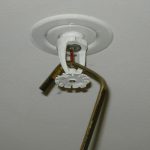
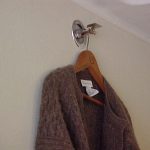
|
- Valves are not closed / opened fully if jammed from dirt or rust – (poor material, raw water, irregular lubrication).
- Valves damaged by mishandling. E. g. use of wrong wrench.
- Valves not properly closed or opened during maintenance/ after testing.
- Valves are misfit – usually due to wrong replacement.
- Gasket / washer not aligned wear and tear with time.
|
|
Missing parts |
- Theft of valve / parts such as hand wheel, padlock, strap etc.
|
|
Automatic valves are more automatic |
- Water pressure that regulates the valve is too low. Should be detected by pressure gauge.
- Leakage through rubber washer which is missing or groves dirty.
|
|
False alarms |
- Retarding chamber or alarm drain leaking
- Supervisory switch tampered by vandalism or mishandling.
- Pressure gauge has loose spring or worn out dial. Accuracy of reading should be tested.
- Pressure regulating valve or switch not calibrated after testing.
- Rusting or wear / tear of flow switch tongue giving wrong signal.
- Misfit flow switch – usually during replacement.
|
|
Low discharge of preaction & deluge valve |
- Drop in supervisory air pressure due to leakage at jointing.
- Diaphragm not opening full if rusted, dirty (esp use of raw water).
|
|
References
[1]
Normative References/Standards Referred to for Air Handling Unit and Fan Coil Unit