Defects
|
Probable causes for the defect
|
Design for Maintainability (DfM) Guidelines
|
Biological fouling of Cooling Tower
Foaming in cooling tower basin
Scale and dirt build-up in fouled fills
Waterfall effect
Algae and dirt promoting bacteria growth
|
- Design is not suitable to prevent dirt accumulation, stagnation.
- Inadequate cleaning of tower fill, basin, drift eliminators etc.
- Inefficient water treatment method used.
|
Design
- Provide a suitable cooling tower design to prevent dirt accumulation and stagnation. (SS 652: DF
- Consider minimising tower fan power and size of towers for close approach as per SS 564-1 in the design scheme.
- Provide automatic chemical dosing systems to ensure access hatches, level indicators, mixers, pumps, etc., can be easily reached by personnel for maintenance and operations. (SS 652: F.1.3.3)
- Specify an automatic chemical dosing system that is capable of checking the conductivity and other required parameters of the CT daily. The automated system with the capability of checking the conductivity and other recommended parameters can be also linked to the building management system (BMS). (SS 652: F.1.3.5)
- Ensure that the CT’s layout has ample space for cleaning so as to prevent bacterial growth. (SS 652: F.1.3.4)
Construction
- Prepare and submit an Operation and Maintenance (O&M) manual for the chemical dosing system after the successful commissioning of the system. (SS 652: F.6.1.4.1)
- Install equipment to routinely observe chemical tank levels and the tank condition of the automated dosing system.
- During installation, ensure that access hatches, level indicators, mixers, pumps, etc. can be easily reached by personnel for maintenance in the operation phase. (SS 652: F.6.1.4.2)
Maintenance
- Perform frequent overall visual inspection and cooling tower sequencing.
- Clean tower fill, basin and drift eliminators. Conduct weekly check on fan motor; clean screen; make up water float and water sampling.
- Conduct monthly check of motor supports, fan blades, motor alignment. (SS 652: F.11.2.1.2)
- Check on condition of bearings and motor, as well as for nozzle clogging, annually. Clean cooling tower at least once a year. (SS 652: F.11.2.1.3)
- Perform monthly check for legionnaire, scaling and corrosion in/of the condenser system. Disinfect and manually de-sludge cooling towers if required.(SS 652: F.11.2.1.4)
- Monitor water usage in Cooling Towers and review the efficiency (SS 652: F.11.2.1.5)
- Ensure optimum scheduling of temporary shutdown and standby of Cooling Towers. (SS 652: F.11.2.1.6)
|
Corroded parts – louver, collection basin


Corroded basin & metal louvers
|
- Material is not corrosion resistant to counteract constant exposure to the condenser water and external environment.
- Damaged protective layer on metallic surface during installation.
- Parts are not cleaned, lubricated or painted in time to prevent corrosion and scaling.
|
Design
Construction
Maintenance
|
Foaming on condenser water

Foaming cond. Water
|
- Too much chemical treatment added.
- Bacteria boom. Cleaning and application of biocide is not done.
- Inadequate access to reach all parts for cleaning.
|
Design
Construction
Maintenance
|
Inadequate heat rejection

Located near exhausts

Waterfall effect
|
- Obstructing structures above the cooling tower.
- Short-circuiting: cooling tower located near heat exhausts.
- Condenser water pump is over supplying – flow rate too high to reject heat properly & waterfall effect.
|
Design
Construction
Maintenance
|
Noise & vibration |
- Mounting on isolator is not levelled.
- Inadequate checking for condition of fan, motor or lack of lubrication.
|
Design
Construction
Maintenance
|
Legionella outbreak
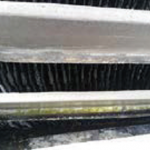 Outbreak on air-water surfaces of Cooling Tower
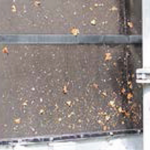 Cooling tower air intake blocked by organic matter
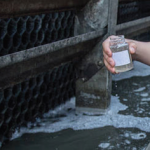 Testing the water for legionella
Algae growth and corrosion of louver — SDE3
|
|
Design
- Avoid redundant pipework, bends, and loops for cooling system design.
- Allow easy access to all parts of the system for maintenance [1].
- Minimise drift by enclosing cooling tower pond.
- Take the wind direction/distribution and the surrounding environment into account when designing the cooling system.
- Use non-corrosive, chemical-resistant, nonporous, smooth, opaque (to block sunlight) material to inhibit growth and proliferation of microorganisms.
- Design of cooling towers must be capable for preventing dirt accumulation and water stagnation.
- Accommodate suitable and efficient water treatment methods in the system’s design.
Construction
- Perform proper commissioning to ensure safe operation of cooling towers. Develop Cooling Tower maintenance manual including cleaning/water treatment/decontamination procedures and handover during commissioning. Ensure system is clear of dirt/debris/organic matter and clean before operation.
Maintenance
- Monitor cooling tower’s water temperature, since elevated temperatures and moisture at air-water surfaces provide ideal conditions that may serve as a nutrient source for legionella growth.
- Check and conform with chemical concentration limits of cooling tower effluents as per local codes and regulations (e.g. Sewerage and Drainage (Trade Effluent) Regulations 1999).
- If cooling tower is not in use, it must be kept drained and dry.
- If not in use for more than 5 days, it should be drained, cleaned and disinfected before operating.
- Conduct regular testing for legionella bacteria, and get water samples from the cooling tower pond (ASHRAE 12-2000, ANSI/ASHRAE 188-2015.
|
References
[1] Institute of Environmental Epidemiology (2001). Code of Practice for the Control of Legionella Bacteria in Cooling Towers (4th ed.). Singapore: Ministry of the Environment.
Normative References/Standards Referred to for Cooling Tower
- ANSI/ASHRAE 188 — Legionellosis: Risk Management for Building Water System
- ASHRAE Guideline 12 — Minimizing the Risk of Legionellosis Associated with Building Water Systems
- SS 564-1 — Green data centres — Part 1: Energy and environmental management systems