Defects
|
Probable causes for the defect
|
Design for Maintainability (DfM) Guidelines
|
Dirty and mouldy ductwork
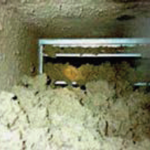 Mould growth in duct
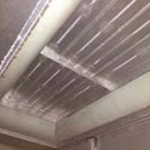 Damper inside AHU collecting condensation, leading to biological growth
|
- Inadequate maintenance or replacement of ducts
- Insufficient access space for cleaning or easy replacement.
- Inefficient cleaning – only the surface row but not the inner rows, where dust and water collects.
- Inadequate duct insulation.
- Poor jointing of ducts, or rough finishes of plenum traps dusts
- Lack of cleaning of ducts – poor access / maintenance.
- Dirty or dusty air flow from damaged or poorly cleaned air filters in AHU.
|
Design
- Conform to the design requirements for air duct systems, including for fittings and accessories, as per SS 553 (where consideration is given to air velocities in ducts, materials and construction method, etc.).
- Fulfil the compliance requirements of thermal insulation for pipework. Comply with the ductwork seal requirements. Ensure that rigid ducts are manufactured from steel, aluminum, glass-fibre or mineral wool, or other approved materials.
- Conform to the minimum duct insulation R-values for cooling supply/return ducts as per SS 553. (See also AS 1668.2).
- Conform If textile based ventilation ducts are selected. Design in accordance with TR 52.
Construction
- Comply with the construction and installation requirements for air duct systems and their fittings and accessories. Ensure that the ducts or duct linings (where glass fibre or mineral wool is exposed to the air stream) are suitably protected to prevent fibre erosion.
- The ducts should be sturdily supported — provide metal hangers and brackets for supporting ducts.
- Guarantee that the inner surfaces of the ducts for supply and return air are smooth and resistant to abrasion in order to reduce dust accumulation (SS 553, AS 1668.2).
Maintenance
- Conduct noise and air loss check when necessary. (SS 652: F.11.4.1.1)
- Perform testing and rating of performance of ducted air-conditioners (ventilation, exhaust and leakage air flow) as per ISO/FDIS 13253. (SS652: F.11.4.1.2)
- Conduct yearly check of ducting insulation. (SS 652: F.11.4.1.3)
- Ductwork hygiene check interval:
- Heavy use (12 – 16 h/day) – quarterly
- Moderate use (6 – 12 h/day) – 6 monthly
- Light use (2 – 6 h/day) – annually
- Perform duct leakage test (for ducts designed to operate at static pressures in excess of 750 Pa) as per industry requirements (SS 553, AS 1668.2).
- Examine internal condition by a Deposit Thickness and/or Vacuum Test and/or Wet Film Thickness Test. If from Wet Film Thickness Test, measurement of > 200 μm as a mean across system is observed, a complete cleaning of the system is required. If a single measurement > 500 μm is observed, an urgent local cleaning is required.
|
Filter media choked at the air terminal
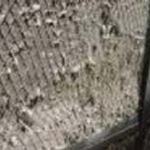 Choked filter
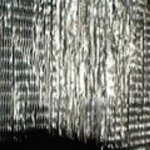 Bent aluminium fin
|
- Intake of dirty / polluted air if inlets are located near exhaust outlet or pollution source such as car parks and cooling towers.
- Inadequate maintenance or replacement of filters
- Insufficient access space for cleaning or easy replacement.
- Problem remains unnoticed if pressure gauge at inaccessible location or above eye level or not calibrated.
- Accidental bending of parts especially fragile fins during installation / maintenance of AHU. Should be combed to rectify.
- Unsuitable chemical cleaning makes aluminum fins brittle.
|
Design
- Provide locations for intake and return air terminals. Conform to the minimum filter requirements with regard to the use of air filters for cleaning outdoor air (MERV) so that no unfiltered air can enter the air handling system.
- Follow the recommended use of a secondary filter of 80% dust spot efficiency (SS 553: 2016, AS 1668.2-2012).
- Provide sufficient access space for easy cleaning and replacement of filters.
Construction
- Conduct alternate efficiency test method for filters (ISO 29463-5: 2011).
- Perform a one-time vet airflow test during commissioning and keep proper record of the report to ensure the cooling capacity is adequate as per design load in accordance to the BCA Green Mark requirement, and that the noise level is within the desired level in accordance to NEA noise pollution standards [1].
Maintenance
- Monitor air pressure and pressure drop across the filter and replace filter when needed. If filter is heavily dented, the filter should be replaced.
- Conduct leakage test to test filter for local penetration ISO 29463 -1:2011.
- Conduct monthly check and observe the dust accumulation level in ducts or grilles.
- Provide a display system for temperature and relative humidity at each floor and at each tenanted area.
|
Condensation on duct or supply air diffuser |
- Insufficient or damaged insulation.
- Leakage of air-duct. It can be trapped in the gaps between fibre insulation and aluminium foil and condensate. Chances are higher if there remains air gap between duct and insulation.
- Diffuser located near infiltration of external air or near entrance.
- Settings of the sensors such as dampers operators and velocity controllers have drifted off, and needs recalibration.
- Inaccessible / access blocked for regular recalibration of sensors.
|
Design
Construction
Maintenance
|
Air Leakage |
- Flanged joints are prone to air leakages.
- The aluminium foil surface is not cleaned before sticking it to the duct tape. The dust works as bond breaker and the joint gets exposed as soon as the foil gets detached.
|
Design
Construction
Maintenance
|
Corrosion |
- Galvanized protection layer cracked or scratched during installation, thus exposing the surface to air and moisture.
- Rainwater entry through fresh air inlet into the supply air duct and this moisture is transported into the ducts.
- Moisture carry-over from AHU transported into supply air ducts.
|
Design
Construction
Maintenance
|
Noisy air flow |
- Turbulence inside under-sized ducts.
- Air not balanced in the ducting system. An opposed blade type damper provides a better option.
- Insufficient or undersized diffusers resulting in high velocity air.
- Malfunctioning of air diffuser dampers. Depends on controls.
|
Design
Construction
Maintenance
|
Poor airflow
Blocked diffuser
High & dirty diffuser
Dumping of cold air
|
- Diffusers located near return air grille cause short-circuiting, diffused air returns before it is circulated in room.
- Diffusers blocked by other installations, furniture layout, wrongly chosen false ceiling.
- Diffuser v dirty, especially of difficult to access.
- Wrong choice of diffusers throws cold air directly at the user.
|
Design
Construction
Maintenance
|
Faulty pneumatic control |
- Pneumatic hoses damaged or leaking pressurized air.
- Failure of air compressor unit – esp. open type.
- Dampers are jammed.
|
Design
Construction
Maintenance
|
References
[1] NUS Maintainability of Buildings (2016). HVAC. Retrieved on January 22 from http:// www. hpbc.bdg. nus. edu.sg/?page_id=94&page=4.
Normative References/Standards Referred to for Air Distribution and Terminal Systems
- AS 1668.2 — The use of ventilation and air-conditioning in buildings — Mechanical ventilation in buildings
- ISO 29463-5 — High-efficiency filters and filter media for removing particles in air — Part 5: Test method for filter elements
- ISO/FDIS 13253 — Ducted air-conditioners and air-to-air heat pumps — Testing and rating for performance
- SS 553 — Code of practice for air-conditioning and mechanical ventilation in Buildings