Defects
|
Probable causes for the defect
|
Design for Maintainability (DfM) Guidelines
|
Physically damaged pipe
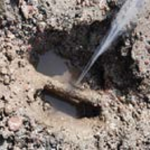 Burst outdoor pipe
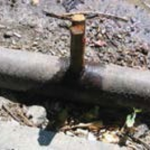 Damaged outdoor pipes |
- Pipe type and joint not suitable for underground condition and suffers from uneven settlement.
- Bursting of pipe under water pressure.
- Inadequate longitudinal support to cater traffic vibration and load.
- Careless backfilling: poor compaction, inadequate depth (<500mm), use of heavy / pointed backfill.
- Work on structure / other services can damage pipes which are too close.
|
Design
- Pipework design should consider factors such as the choice of material, rate of flow, accessibility, protection against damage, corrosion, avoidance of airlocks, water hammers, noise transmission, unsightly arrangements, vibration and expansion of fluid, stress and strains, etc. (BS EN 1057:2006+A1:2010, BS EN ISO 21003-2: 2008+A1:2011, BS EN ISO 21003-3:2008, BS EN ISO 21003-5:2008).
- Provide adequate longitudinal support to pipe installations below ground to cater for loads and traffic vibration.
Construction
- For underground pipe laying, bedding should be fully compacted prior to installation and the correct depth of trench, gradient, width and bottom condition should be maintained.
- Properly align pipe work and use suitable joints. Ensure careful backfilling at an adequate depth for underground pipe laying.
- Completed sections should be tested for defects using leakage tests and should be rectified by the contractor as required.
- Maintain proper water pressure in piping system to avoid bursting from over pressurisation.
Maintenance
- Conduct thorough cleaning and disinfection of service pipes on a monthly basis, and clean the main pipes semi- annually. If required, removal of blockagewith manual cleaning method (e.g. plunger, drain rod, spring auger) should be performed.
- Conduct chemical de-scaling quarterly (care should be taken so that it does not harm the pipes or jointing by giving consideration to chemical type or contact time).
- Perform maintenance schedule to check for clogged outlets (BS 8558:2015, SS CP 48:2005, see also [5]).
|
Degraded pipe: rusting, pitting etc.
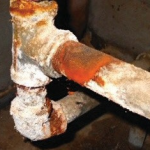 Corroded galvanised piping
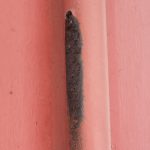 Corroded down pipe |
- Material corrodes in contact with surrounding / supports.
- Protective coating damaged during careless installation – integrity not tested.
- Wearing of external protective coat of metal pipe expose it to electrolytic and atmospheric corrosion.
- Aging, hardening of PVC pipe under prolonged exposure to sun.
- Thermal stress from close proximity of hot water pipes if limited freedom for thermal movement provided.
|
Corrosion and scaling of pipe/valve
 Scaling in pipe
 Corrosion of pipe flange |
|
Design
- Specify materials that are resistant to corrosion and non-reactive to the conveyed water and surrounding ground (BS EN 545:2010, BS EN 598:2007+A1:2009), and that do not impart any taste or toxicity to the water (BS EN 1796:2013, SS 375-1: 2015).
- Use of single material for the entire system is preferable for easy connection/jointing. Specify pipe system material that does not react with the pumped medium.
Construction
- Pipe penetrations and joints should strictly comply with manufacturer’s instructions.
- Jointing material should not enter pipe. Caulking at penetration sleeve should be made watertight.
- Fulfill proper installation while ensuring that the protective coating is not lost/damaged during installation (BS 8558:2015, SS CP 48:2005).
Maintenance
- Conduct quarterly chemical and bacteriological analysis of water used [12].
- Perform monthly check of water supply for visual signs of leakage, scaling and corrosion of pipes, joints and valves. Increase frequency of inspection for damp or polluted areas (BS 8554:2015).
- Conduct monthly inspections and clean off/remove any rust or scale. Re-paint parts in a timely manner if needed (BS EN 806-5: 2012).
|
Leakage at joints
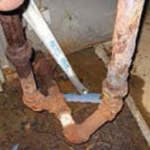 Leaky pipe wetting the floor
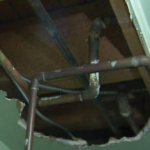 Ceiling damaged by pipe leakage due to haphazard pipe laying
|
- Pipe joints are not properly finished or wrong jointing method adopted.
- Joining pipe of two different materials is inherently week.
- Valve stems are not fitted tightly with gasket / washer (missing).
|
Design
- Conform to the pipe sizing requirements based on hydraulic design and pump performance.
- Provide allowance for head loss, and frictional loss due to internal roughness, loss at fittings, turbidity, surge and pumping facility.
- Do not oversize piping as slow flow will cause stagnation.
- Specify standard fittings such as tees, elbows, etc. (BS 7291-1:2010, BS EN 598:2007+A1:2009, BSEN 545:2010).
Construction
- Comply with the installation of water fittings as per PUB guidelines as stipulated in SS CP 48:2005. (See also BS 8558:2015).
- Fittings that are fabricated by welding together segmented pieces are not recommended.
- Avoid haphazard pipe laying.
Maintenance
- Perform thorough investigation to check compliance with SS CP 48: 2005, and BS 8554:2015.
- Conduct monthly inspection of water flow rate and pressure, and position and functioning of valves.
- Conduct maintenance inspections of the pipe installation and identify/rectify physical defects such as broken pipe braces, dents, or leaks. (See also BS 8558:2015, BS EN 806-5:2012).
|
Noisy / turbulent flow/ water hammer
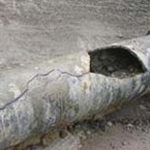 Cast iron pipe cracked by water hammer
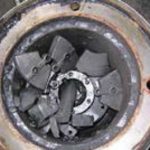 Thrust bearing of a submersible pump ruined by water hammer |
- Design details unable to prevent water hammer or splashing.
- Inadequate support / anchor blocks at every bend, branch & dead-end results in hydraulic thrust.
- Airlocks : Low supply pressure,
|
Design
- Pipework design should avoid water hammers (water pipe banging) (JIS A 4422:2011, BS EN 1057:2006+ A1:2010).
- Design airlocks and low supply pressure to minimise turbulent flow.
- Evaluate the required strength of valves and tightness of body and in between the inlet and outlet chamber as per BS EN 1567:1999.
Construction
- A water hammer may arise when the electric valves on appliances or single control valves are shut off fast. Although all noises due to water flow and pipe expansion cannot be removed, the contractor is responsible for fastening the pipes properly and commissioning valves/ actuators to minimise the water hammer.
- Install check valve to control the creation of a vacuum in discharge pipe (BS EN 16767:2016, BS EN 545: 2010).
Maintenance
- Conduct monthly pressure test by operating pump for min. 1 hr with 125m head or 150% of working pressure (whichever is greater) and check for any individual leakage or overall leakage.
- Conduct semi-annual pressure test for sewage pumps.
- To rectify water hammer issues, provide additional bracing or anchor block support at bends and branches in order to withstand the hydraulic thrust.
|
Difficult Maintenance/ leaky joints in inaccessible areas
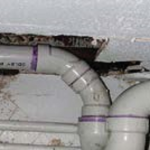 Leaking pipe above ceiling
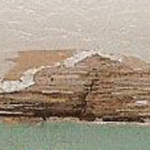 Leaky water pipes in the ceiling |
- Pipes are difficult to access if laid at a depth more than 2m below ground; covers of pipe work are not easily removable or embedded in structural element or insufficient servicing space.
- Haphazard layout – poor design or non-compliance with drawing.
- Interrupted supplies during repair –stop valves at every level or at convenient places / on branch pipe are not planned. Hence repair at one part disturbs supply to other parts of building.
|
Design
- Adhere to the recommended requirement to maintain sufficient distance (> 400mm) from structure or other services running parallel to each other, for easy maintenance and to avoid interference or damage.
- Pipes should be of adequate strength and durability, and adequately supported (BS 8558:2015, SS CP 48:2005).
Construction
- Ensure that the pipes and fittings are stored and installed as per manufacturer’s instructions.
- Prevent any interior contamination. If contamination occurs, clean before installation.
- Take special care when joining two dissimilar materials.
Maintenance
- Perform routine monitoring of piping system and check for any possible water seepage through the building fabric (BS 8558:2015, BS EN 806-5:2012).
- Repair the pipe joints properly using the correct jointing method.
- Tighten valve stems by replacing/fitting any missing gasket/washer.
|
Inadequate/ poor supply |
- Faulty design to calculate demand, diameter of pipe etc. Also allowance for frictional head loss, bends, and fittings should be considered.
- Direction of flow against hydraulic gradient.
- Excessive friction loss in pipes with very rough inner surface (poor make) or at joints which are not finished smooth or have projections.
- Oversized pipe or under capacity pump unable to deliver right pressure.
- Loss of pressure by faulty pumps. Regular testing can detect the fault.
- Hunched pipes, wrong hydraulic gradient or wrong size of valve orifice cause airlock.
- Dirt accumulation at joints – bad fixing detail, and irregular flushing.
- Excessive leakage at pipe joints (E4).
|
|
Contamination- users fall sick |
- Interference with potable and non-potable water due to poor planning/ workmanship. E.g. sewers placed above supply lines.
- Wrong position of draining tap allows drained water in certain parts of the building interferes with the supply to other parts of the building.
- Unsuitable material for pipes / joints (e.g. lead found in old bldg).
- Ligionella growth esp in hot water pipes if temp. doesn’t reach 60° C. Water analysis can put a check on contamination.
- Water stagnation or dirt accumulation at pipe joints due to wrong detailing, poor finishing of joints.
- Dirt enters by wall seepage or with dirty testing tools.
- Stagnation inside large tanks if outlets are not diagonally opposite to the inlets. Lack of ventilation aggravates the problem.
- Inside tanks, mosquito breeding, entry of other creature, leaves, dust causes contamination. Omitted / damaged net at overflow and vent pipe or the cover is left open after maintenance.
- Corrosion leaky / ruptured pipe passing through contaminated soil or penetration at underground reservoir is leaky.
- Seepage through pipe joints that are not strong and water tight (wrong jointing method / poor workmanship).
- Irregular cleaning of tanks or flushing of distribution pipes. This problem is more frequent if cleaning is difficult (E7).
- No flush out points at the end of distribution pipes.
- Back flow and back siphonage happens due to wrong detailing (e.g. for tanks inlet pipes are at lower level than the overflow pipe).
|
|