Defects |
Probable causes for the defect |
Design for Maintainability (DfM) Guidelines |
Vibration and noise |
- Overloading – fluctuation density of core.
- Loose connection of bolt on clamping structure. Use of wrong sized crimp or improper tool.
- No precaution of sound isolating pad / vibration damper for mounting.
|
Design
- Comply with the requirements of electrical installations as per BS 7671:2008+A3:2015, SS CP 5:1998, NFPA 70 [5]; including the location and number of power points.
- Ensure switchboards have adequate space and access for operation and maintenance.
- Specify suitable switch closets with regard to moisture exposure conditions.
- Refer to the definition of types and functionality of RCCBs and specifications for RCBOs as per SS 480:2016 (IEC 61009-1:2010+AMD1:2012+AMD2:2013 CSV BS EN 61009-2-1:1995).
- Provide sub-metering system with remote measurement capability and link to BMS/EMS to track energy consumption data trends [6].
Construction
- Conform to the guidelines for construction and compliance inspection of electrical connections and earthing thereof (BS 1363-4:2016, SS 403:2013).
- Refer to BS 8512:2008 for storage, handling and installation of power cables on wooden drums.
- Install sub-metering system with remote measurement capability and link to BMS/EMS to track energy consumption data trends [6].
- All accessible metal parts of connection units should be in electrical contact with the earthing terminal(s) (BS 1363-4:2016, SS 403:2013).
Maintenance
- Conform to the maintenance of electrical installations as per BS 6423:2014, BS 6626:2010, SS 538: 2008, [3;7].
- Check for insulation damages (e.g. cracks, blisters, warping) caused by overheating, physical impact or by spillage of cleaning chemicals.
- Check for potential short circuits or ground faults. Ensure that switchboards are not exposed to direct sunlight or alternative heat sources.
- Conduct annual shutdown to eradicate hot spots along the distribution network as witnessed by the owner and certified by a Licensed Electrical Worker (LEW).
- Provide necessary warning notices/labels at switchboards (e.g. shock hazard warnings).
|
Overheated or burnt parts body, feeder etc.
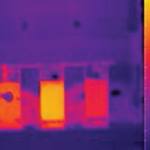 Hot connector (thermal image |
- Insufficient air ventilation in the room or heat dissipation.
- Loose or wrong sized parts increase resistance.
- Over greasing, lack of training & proper tool causes loose connections
- Eddy current, excessive overloading.
- No thorough investigation to detect the problem in inner parts.
- Dirt, grime from insulation and windings prevents heat dissipation.
|
Oil leakage |
- Foreign make – not suitable for higher ambient temperature of tropics.
- Careless lubrication.
- Excessive corrosion overlooked for a very long time.
|
Damaged insulation |
- Damage during transportation is not checked before installation.
- Poor cleaning – often hindered by poor access.
- High acidity of cooling liquid. Should be checked and changed.
- Breakdown of insulation from overheating.
|
Unsuitable / unsafe working condition
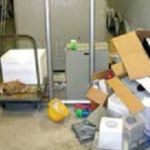 Room used as storage for combustible materials and other equipments
Worn protective mat
|
- nsufficient space design or transformer room used as storage.
- Protection mat deteriorated with time or spillage of chemical.
- Inadequate lighting and ventilation.
- Slippery, dirty floor surface from oil spillage, scattered parts.
- Omission or missing warning sign or locks.
- Door mechanism of transformer room is not set to de-energize transformers upon opening the door.
|
References
[1]
Normative References/Standards Referred to for Air Handling Unit and Fan Coil Unit