Problem |
Design for Maintainability (DfM) Guidelines |
Compromised/poor
condition of elevator
 Leaking ceiling of the machine room
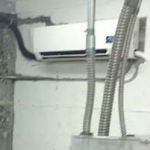 Good practice: Installing a cooling system in the machine room to prevent excessive heat in equipment |
Design
- Comply with local codes, and consider elevator system performance (SS 550:2009, CIBSE Guide D [14], BS 5655-6:2011, BS 5655-11:2005, BS EN 81-20: 2014).
- Provide ease of access to the elevator machine room with outward opening door (minimum clear opening of 0.6 × 1.8m) and permanent safe access for personnel and heavy equipment.
- Machine room should be equipped with electric lighting with a minimum illuminance of 200 Lux at floor level. Also provide switched
socket-outlets. (BS 5655-6:2011, BS 5655-11:2005, BS EN 81-20: 2014, SS 550:2009).
- Provide good ventilation to the machine room (natural or mechanical). For natural ventilation, a 20% opening of the floor area is recommended to achieve cross-flow.
Construction
- Provision for mechanical ventilation is recommended when the ambient temperature of the room exceeds 32°C. (BS 5655-6:2011, BS 5655-11:2005, BS EN 81-20:2014, SS 550:2009).
- Properly commission elevator prior to operation as per BS 8486- 1:2007+A1:2011. Lift machine and drive must be securely mounted. All movable parts, the gear box, and joints should be sufficiently lubricated [13].
Maintenance
- Conduct regular inspection of room condition and practice proper housekeeping. The room should not be used as storage; remove all non-elevator related materials from the machine room. Adequate lighting should be provided in the elevator machine room to allow workers to conduct maintenance works safely and efficiently [14].
- Machine room should be ventilated to ensure the temperature difference measured at any point within 1000mm of machinery and associated equipment does not exceed 380C (BS 5655-6:2011, BS 5655-11:2005, BS 7255:2012, BS EN 13015: 2001+A1:2008, SS 550:2009).
|
Poorly-maintained
elevator pit
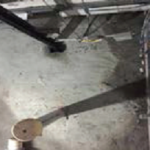 Leaking elevator pit |
Design
- Ensure proper waterproofing design of elevator pit (BS 5655-6:2011, BS 5655-11:2005, BS EN 81-20:2014, SS 550:2009).
- Specify corrosion resistant material and components in elevator system to minimise damage by presence of water or excessive moisture.
Construction
- Test waterproofing of elevator pit before installation of elevator equipment (BS 5655-6:2011, BS 5655-11:2005, BS EN 81-20:2014, SS 550:2009).
- Avoid any damage to waterproofing membrane during elevator installation.
Maintenance
- The pit areas should always remain dry. If there is any presence of water, the source of water must be identified and eliminated.
- Conduct routine inspection of the elevator pit for water seepage due to faulty waterproofing membrane.
|
Faulty door operation
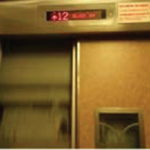 The elevator inner doors failed to close completely during operation (Photo credit: Ben Tng, 2016)
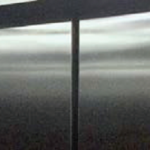 Jammed elevator doors do not close completely |
Design
- The gap for the elevator car doorway must not exceed 12mm, and the clearance between elevator car door panels must be less than 10mm. The elevator car must not make any movement if the car doors and landing doors are not properly closed and locked [13].
- Use durable materials for the doors and more durable materials for their frames (e.g. metals) (BS 5655-6:2011, BS 5655-11:2005, BS EN 81-20:2014, SS 550:2009).
Construction
- Test elevator car and landing doors to withstand an impact that is similar to the impact when a person collides with the door at running speed (BS EN 81-20:2014).
- The main guiding elements of door should operate as intended. Doors must include retainers to keep the door panels in place (BS EN 81-20:2014).Partially-closed door must open (if button controlling door opening is pressed); while the door must remain open when the door open button is pressed [13].
Maintenance
- Inspect elevator door and guides, shoes, and tracks. It should not show any permanent deformation or elastic deformation not greater than 15mm (when force of >300 N is applied to 5cm2 area at centre of door panels at a right angle) (BS 5655-6:2011, BS 5655-11:2005, BS 7255:2012, BS EN 13015:2001+A1:2008, SS 550:2009).Review the service call frequency for the door.
- Increased service calls signify the need to upgrade/replace door operators.
|
Lift lobbies with poor
accessibility for the
disabled
 Good practice: Design a wheelchair accessible lift lobby (photo shows an example from a residential building) |
Design
- Encourage through or two-end entries for lift lobbies; or provide added space for deadend lobbies to ensure the better distribution of waiting passengers (BS 5655-6:2011, BS 5655-11:2005, BS EN 81-20:2014, SS 550:2009).
- Provide rain covers for lift lobbies in residential buildings for protection from torrential rains.
Construction
- Install lift lobby pedestrian flooring as per recommended minimum pendulum ratings specified in SS 485:2011. (See also AS HB 197:1999 and AS/NZS 4663:2004).
Maintenance
- Practice proper housekeeping to keep the lift lobbies clean and clear of dirt, and avoid any obstruction or stacking to accommodate easy egress and ingress.
- Conduct routine inspection of lift call buttons and indicator displays; check that they are in acceptable working condition.
|
Inaccurate elevator car
levelling with the
landing
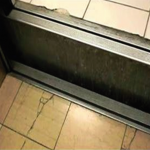 Elevator car is not levelled with the landing floor
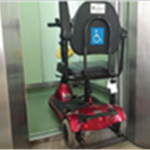 Poor levelling can cause trip hazard |
Design
- Comply with the design guidelines for permanently installed electric lifts as per SS 550:2009, CIBSE Guide D [14] (BS 5655-6:2011, BS 5655- 11:2005, BS EN 81-20:2014) [15].
- The stopping accuracy of the elevator car against the landing floor must be ±10mm [13].
- Collate global standards on lift safety as per ISO/TR 11071-2:2006 (i.e. assumption of safe operation assured to 125% of rated load, assuring reliability of lectric safety devices, mechanical devices built and maintained according to good practice).
Construction
- Conform to the guidelines for construction and installation of permanently installed electric lifts as per SS5 50:2009, BS 5655-6:2011, BS 5655-11:2005, BS EN 81-20:2014.
- Adhere to the safety rules for construction as per BSEN 81-50:2014.
- Every lift must be provided with a capacity te located in a conspicuous place inside the car, indicating the rated load in kilograms and, in the case of passenger lifts, the maximum number of passengers to be carried (BS 5655-6:2011, BS 5655-11:2005, BS EN 81-20:2014, SS 550:2009).
Maintenance
- Upgrade the control system, braking, and motor types. A microprocessor controller will electronically monitor and control motor rotation to ensure that the elevator car accurately stops at floor
level.
- Review levelling of car to ensure the value is acceptable by standards
to avoid risk of passengers tripping and falling (e.g. wheelchair users)[13].
- Permit to operate (PTO) to be displayed in the lifts [13].
- Measure ride quality of elevators as per BS ISO 18738:2003.
|
Compromised safety and reliability
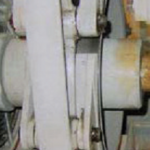 Dirt and rust in machine
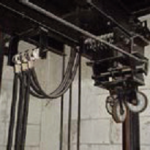 Corroded guide rail |
Design
- Specify electronic components for elevator system reliability (BS 5655-6:2011, BS 5655-11:2005, BS EN 81-20:2014, SS 550: 2009).
- Ensure compliance to global essential safety requirements (GESRs) for lifts and local safety standards as per ISO/DTS 8100-21.
- Lift must be designed to ensure all lift parts do not affect safe operation under reasonable levels of depreciation [13].
Construction
- Map out safety checks for lifts and classify them according to safety and comfort requirements. Safety gear must be able to stop/hold lift car and counterweight within allowable distance as per SS 550:2009. (See also BS 5655-6:2011).
- Proper installation and commissioning of Emergency Battery Operated Power Supply (EBOPS) of lift car, braking system, call buttons, load alarm, safety switches functions, safety logic, emergency lighting and supply, etc. [13].
Maintenance
- Conduct conformance test for electronic components of lift machines which are susceptible to damage from high temperatures that may impair reliability (ISO/TR 25743:2010).
- Conduct monthly safety levelling of the car and landing.
- Follow the mandatory incident reporting procedure in the case of an accident/incident [13].
|
Faulty suspension ropes due to overloading
 Broken suspension ropes
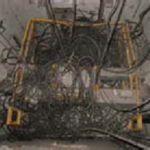 Elevator suspension ropes severely damaged |
Design
- Comply with the design requirements for rated loading capacity as per
SS 550:2009 (BS 5655-6:2011, BS 5655-11:2005, BS EN 81-20:2014).
- Adhere to the guidelines for lift installation as per ISO/CD 8100-30, ISO 7465:2007, ISO 14798:2009, ISO/NP TR 16765.
- Provide a lift monitoring system to enable remote tracking of lift breakdown.
- Consider designing separate service and passenger lifts.
- Specify durable materials for service lift floor and walls to withstand rough usage.
- Overload weighing device should be provided and must activate an alarm when the load in the car exceeds the rated capacity (BS 5655-6:2011, BS 5655-11:2005, BS EN 81-20:2014, SS 550:2009).
- Install suspension ropes as per ISO 2408:2004, BS EN ISO 16841:2014 and ensure it is properly and equally tensioned. If rope is damaged during installation, even if it passed tests prior to elevator service, the damaged rope should be replaced with a new rope, instead of just replacing the strands (ASME A17.6-2010).
- Lift capacity rate should be located at a noticeable position in the elevator car. It should indicate the rated load in kilograms and state the maximum number of passengers.
Maintenance
- Periodic maintenance should be done by a BCA registered lift contractor at intervals not exceeding one month. An annual inspection and system test should be done by an independent Authorised Examiner (AE). Adhere to the guidelines for the operation and maintenance of permanently installed electric lifts as per SS 550:2009. (See also BS 5655-6:2011, BS 5655-11:2005, BS 7255:2012, BS EN 13015:2001+A1: 2008).
- Conduct annual test of safety equipment without load. A full load test should be conducted every 5 years. Sufficiently lubricate ropes frequently to avoid abrasive wear between and within the strands. Ensure the timely replacement of ropes if they are permanently kinked, bent, or deformed as per criteria set out in ASME A17.6-2010.
- Lift ropes shall be tested against requirements of ISO 4344:2004 for signs of excessive wear and tear.
|
Failure to activate
overspeed governor
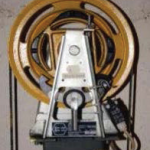 Example of a typical overspeed governor (Photo credit: Jones, I. G. et al., 2013) |
Design
- The governor ropes should be made from iron, steel, Monel, metal, phosphor bronze or stainless steel (ASME
A17.3-2008).
- The governor rope’s diameter should be at least 6mm (BS 5655- 6:2011, BS 5655- 11:2005, BS EN 81-20:2014, SS
550:2009).
- The electrical and mechanical tripping speeds should be in accordance with the requirements of SS 550:2009 (BS 5655-6:2011, BS 5655-11:2005, BS EN 81-20:2014).
Construction
- For safety code for the construction and installation of the overspeed governor refer to BS EN 81-50:2014.
- For the type of examination for overspeed governors, refer to BS EN 81-50:2014, which requires a minimum of 2 tests conducted with 0,9 — 1,0 gn acceleration to check the strength of the overspeed governor.
- Comply with BS EN 81-50:2014 for tests of tripping by breakage of suspension means.
- Commissioning to ensure that overspeed governor functions as intended, for safety under all operating conditions [13].
Maintenance
- Inspect the general condition of the speed governor, governor rope and diameter, tripping mechanism and governor switch and governor data plate with no power.
- Inspect overspeed governor under normal running conditions with power on (BS 5655-6:2011, BS 5655-11:2005, BS 7255:2012, BS EN 13015:2001+A1:2008, SS 550:2009).
- Governor rope should not show any sign of excessive wear and tear, in accordance with the requirements in ISO 4344:2004.
|
Inefficient energy
performance
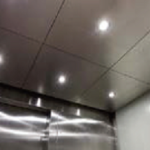 Good practice: application of LED lighting fittings in an elevator car
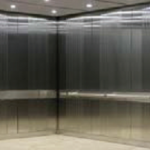 Good practice: use of stainless steel finishing to maximise illumination in car (by reflecting light). Also results in a more durable elevator car |
Design
- Select and design lift equipment that will cater to expected traffic needs with energy efficiency, as attained by proper equipment management (BS 5655-6:2011, BS 5655-11: 2005, BS EN
81-20:2014, SS 550:2009).
- Conform to the energy calculation and classification for lifts as per ISO 25745-2:2015.
- Comply with the minimum energy efficiency requirements as per SS 530:2014.
- Refer to planning for energy efficiency of lifts and escalators to VDI 4707.
Construction
- Fulfil energy performance and verification of lifts as per ISO 25745-1:2012.
- Install luminaires which adhere to the maximum lighting power density for lift lobbies; i.e. 7 W/m2.
- Install equipment to measure energy consumption on installed equipment of lifts with reference to ISO 257545 series (Part 1, Part 2 and Part 3). (Refer also to SS 530:2014).
Maintenance
- Comply with the measurements of energy consumption.
- Conform to the energy calculations and classification of escalators and moving walks as per ISO 25745-3:2015.
- Conduct regular maintenance of the equipment to ensure moving parts are sufficiently lubricated and to identify early signs of wear and tear for timely corrective action and efficient equipment usage.
- Perform timely modernisation to enhance performance/energy efficiency (BS 5655-6:2011, BS 5655-11:2005, BS 7255:2012, BS EN 13015:2001+ A1:2008, SS 550:2009).
|
Poor/compromised
lighting
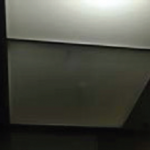 Burnt out elevator car lighting bulb |
Design
- Lift car should be provided with permanently fixed electric lights (no less than two lighting fittings per car to be provided).
- Ensure lighting intensity of at least 50 lux at floor level (BS 5655-6:2011, BS 5655-11:2005, BS EN 81-20:2014, SS 550:2009).
Construction
- Install emergency luminaires in lift cars in accordance with SS 550:2009 (BS 5655-6:2011, BS 5655-11:2005, BS EN 81-20:2014).
- Use energy efficient lighting with sensors during installation for energy efficiency.
Maintenance
- Ensure that luminaires are protected to prevent injury of passengers from breakage; and to prevent access to live parts by passengers (BS 5655-6:2011, BS 5655-11:2005, BS 7255:2012, BS EN 13015:2001+A1:2008, SS 550:2009).
|