Case 6
- Introduction
- Causes of Defects
- Good Practices
- Standards
- Maintenance and Diagnostics
- Remedial
- Similar Cases
- References
Good Practices
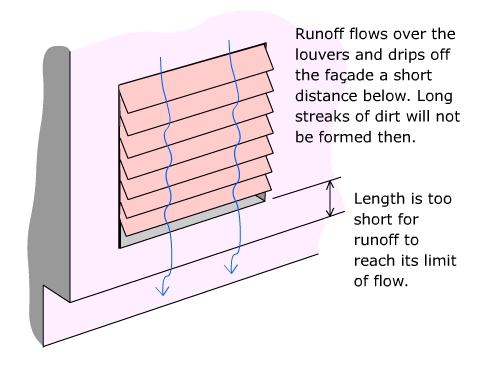
Louvers are incorporated usually for the functional purpose of exhausting air within spaces in the building to outside the building. If required to make up part of the façade, they should ideally be located near to ground level or located such that there is not a wide expanse of façade beneath it. By doing so, there would then not be sufficient area for the runoff to reach its limit of flow of runoff and thus dirt would not be deposited (Figure 3). This may involve re-evaluating the location of machine rooms and other service rooms.
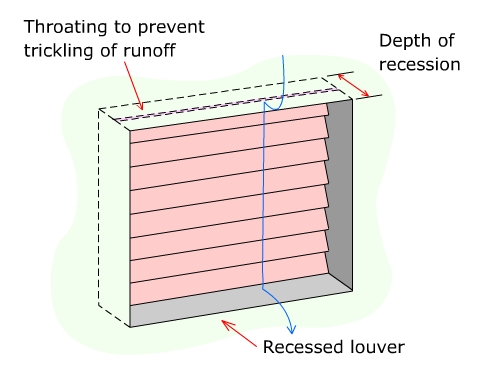
Louver units could also be recessed deep into the façade so that runoff flowing down from above will not run over the louvers and driving rain could not impact on the louver unit. Small louver units could be sheltered in this manner (Figure 4) but for large louver units, the depth of recession may be too large and thus might not be feasible. Still, by recessing the louver unit, runoff flow from above can at least be kept out and the rate of stain formation would be reduced.
Design
Specify material and application methods for water repellence of porous masonry in accordance with BS 8221-2, SS 509-2 or equivalent. Throw off water from the façade altogether through an outward projecting sill or overhanging eaves (which incorporate a throat or drip lines on its underside) or provide blocking features such as copings/flashings. Use efficient scupper drains/downpipes to channel water down and away from the façade. To provide drip grooves along the underside of projecting features. Specify a paint system, which is permeable to avoid any paint defects which may cause staining.
Render the detailing for open joints as opposed to butt joints to avoid sealant staining. To use nonbleed sealants so as to prevent staining from silicone oil. Recommend joint designs, which are able to retain rainwater runoff within joints and expansion joints designated to provide vertical runoff carrying dirt down along the façade surface. Specify façade self-cleaning applications (e.g., TiO2, superhydrophobic
paint products, etc.) with due consideration given to site orientation, sunshades and protruding features. To understand the impacts of environmental, material, design and maintenance aspects on rainwater runoff.
See also Staining of Facades
Construction
Paint façade surfaces evenly with no patchiness. The finished texture should be uniform in colour. Ensure proper rendering to control surface granularity and local faults as it influences colour uniformity of the external façade in accordance with ISO 7361 or equivalent. Correct sealant applications to ensure consistent and continuous quality. Avoid misaligned panels of cladding in accordance with BS 8000-0 or equivalent. Refer to the planning of the painting programme, including inspection regime (initial and routine inspections) for buildings in accordance with BS 6150, SS 542 or equivalent.
Use self-cleaning coatings on newly built substrates for increased success in its performance. All construction/repair works on a façade surface should be done prior to application of a water repellent in accordance with BS 8221-2, SS 509-2 or equivalent. For serviceability of exterior façade surfaces, adopt ASTM E1667-95a or equivalent. It is important as it dictates the building’s individual and corporate identity. The correct application of TiO2 coating is crucial to ensure proper adhesion to the substrate. It is also challenging to check the proper application of the coating, especially on high-rise buildings, due to
its transparent property.