Case 2
- Introduction
- Causes of Defects
- Good Practices
- Standards
- Maintenance and Diagnostics
- Remedial
- Similar Cases
- References
Good Practices
Sealants used shall be of suitable type to form a seal against water and air penetration and to withstand stresses during assembly, transportation, installation and operation of the curtain wall system. Sealants displaying predominantly elastic characteristics are recommended such as polysulphides, polyurethanes, silicones or other materials approved by the Specifying Authority.
When sealant is required to seal a joint between two different substrate, its compatibility with both substrate must be considered.
A good understanding of a joint sealant system is required especially for facade exposed to harsh outdoor environmental conditions subjected to cyclical temperature and moisture changes, thermal shock etc.
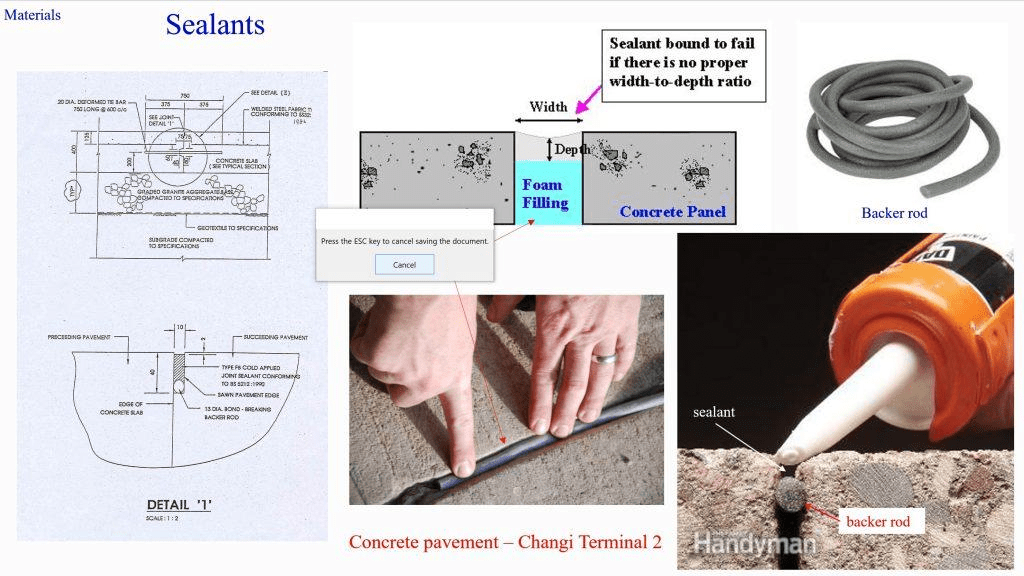
For this case, the reasons for the joint failure include:
- Poor workmanship in applying the sealant to joints due to lack of skillful labour
- Poor material selection for the sealant
- Water can dissolve the chemicals which thus make the sealant softened and lose its elasticity.
- Solvent evaporation
- Ozone attack, migration of plasticisers
- ultra-violet radiation
- Joint design: incorrect type of joint required with respect to dimensions, locations, joint spacing related to expected movement, shape and nature of backing material.
Also to note:
- Sealants used shall be of suitable type to form a seal against water and air penetration and to withstand stresses during assembly, transportation, installation and operation of the curtain wall system. Sealants displaying predominantly elastic characteristics are recommended such as polysulphides, polyurethanes, silicones or other materials approved by the Specifying Authority.
- Some cladding systems employ open joints concept allowing wind-driven rain and panel surface flow to enter the horizontal and vertical joints, which acts as a drainage system and discharge water away (Figure 1). Sealant is not required and thus sealant defects can be avoided. Other cladding systems have joints protected by gaskets instead. Open joint systems that use sealant that is recessed into the joint can protect the sealant from direct exposure to environmental elements such as ultraviolet rays (Figure 2). This may help to increase the durability of the sealant as compared to joints where the sealant is flushed with the panel surface allowing it to be directly exposed to ultraviolet radiation.
- Use capping to protect the sealant joint. This will ensure that no chemical reaction will take place at the sealant joint.
- Workmanship on-site should be ensured so that good designs are properly executed. Care should be taken when applying sealant so as to prevent dirt from being attracted onto the metal surface. Sealants should be applied to dry, non-greasy surfaces.
- A maintenance schedule could be worked out so that the façade is cleaned periodically with cleaning agents recommended by the façade manufacturer.
- Sealants must be continuous and of consistent quality.
- Avoid bridging angles, particularly with mastic strip sealants. Apply extra thickness at corners as a precaution.
Design
Select sealant joint type and mode of application in accordance with BS 6213 or SS 654; including requirements for quality management programme. Adopt the guidelines on the selection of construction sealants in accordance with BS 8221-2, SS 509 or equivalent. For grading of sealant (i.e., pourable or non-sag), refer to ASTM C920-18 (tested), ASTM C639-15 or equivalent. Make provisions for access for regular sealant inspection and avoid placing design features/services across joints that impede access for maintenance.
Construction
Apply sealants in accordance with recommended guidelines in BS 8000-0, BS 6093, SS 654 or equivalent. Perform dynamic peel test and dynamic tensile test on structural sealants in accordance with ISO 28278-2 or equivalent. Carry out non-destructive and destructive inspection procedures of weatherproofing sealant joints in accordance with ASTM C1521-19, BS EN 15651-1 or equivalent. Use a two-cloth method to properly clean and prime.