Case 1
- Introduction
- Causes of Defects
- Good Practices
- Standards
- Maintenance and Diagnostics
- Remedial
- Similar Cases
- References
Maintenance and Diagnostics
Carry out appropriate maintenance of the fenestration product and its interfaces with the wall system to ensure long-term delivery of the desired water penetration resistance. Maintain records of building use, maintenance and performance problems, as well as responses to those problems in accordance with ASTM E241-09.
In general, good quality concrete does not require extensive maintenance. However, due to external factors it might have some defects even before reaching its design life.
Regular inspections and checking should be conducted at regular intervals to detect these defects and to take remedial action to remove these defects. An efficient inspection system should be adopted to ensure the conduct of regular checks such as visual inspections periodically.
Regular inspection should be carried out in accordance with BS 8210 to identify defects and ensure repair work is carried out before associated damage can occur. Testing of concrete via depth of carbonation
should be carried out to identify possible corrosion of rebar in accordance with BS 1881-210 or via the
phenolphthalein method in accordance with BS EN 14630 or equivalent. Damaged concrete due to
corrosion of reinforced steel should be repaired and protected in accordance with BS EN 1504-9 or equivalent.
Suitable instruments and techniques should be used to diagnose defects properly. Diagnosis involves a process in which experts investigate the buildings’ conditions, carry out tests, evaluate, make recommendations for remedial actions where necessary and predict the future performance of a building.
Diagnostics of Defect (see also NDT)
Visual Inspection
Visual assessment evidence is brown staining that may had permeate to the concrete surface without cracking of the concrete but usually it accompanies cracking or cracking of the concrete will happen shortly thereafter. For spalling the following information should be noted:
- Extent and number of affected areas
- Depth of failure
- Degree of detachment
- State of reinforcement corrosion
- Surface discolouration effects
Carbonation Test


Spray concrete surface with phenolphthalein indicator, which registers a strong pink colour if the concrete retains its alkalinity.
Depth of carbonation is the location of the carbonation front and its proximity to the bars.
If the average carbonation depth approaches the average cover depth, more steel will start to corrode.
Half Cell Potential Measurement
The main application of Half cell measurement is to evaluate the probability of corrosion of the steel reinforcement embedded in the concrete members. This is measured in relation to the potential value readings.


Profometer (Covermeter) – rebar scanner
Profometers (covermeters), based on the principles of electromagnetism, are use to locate and to measure the depth of rebar (concrete cover).

Eddy Current Test
Eddy Current NDT is an inductive technique which employs a probe (coil with a AC current) placed close to the inspected material. When an AC current flows in a coil in close proximity to a conducting surface the magnetic field of the coil will induce circulating (eddy) currents in that surface.
The primary flux in the Figure above induces eddy currents in the material which give rise to a secondary flux. The secondary flux is then coupled back to the coil which affects its impedance. Thus the magnitude and phase of the eddy currents will affect the loading on the coil and thus its impedance. If a discontinuity (defect) is present in the material the eddy current density will be changed which can be observed as a change in coil impedance.
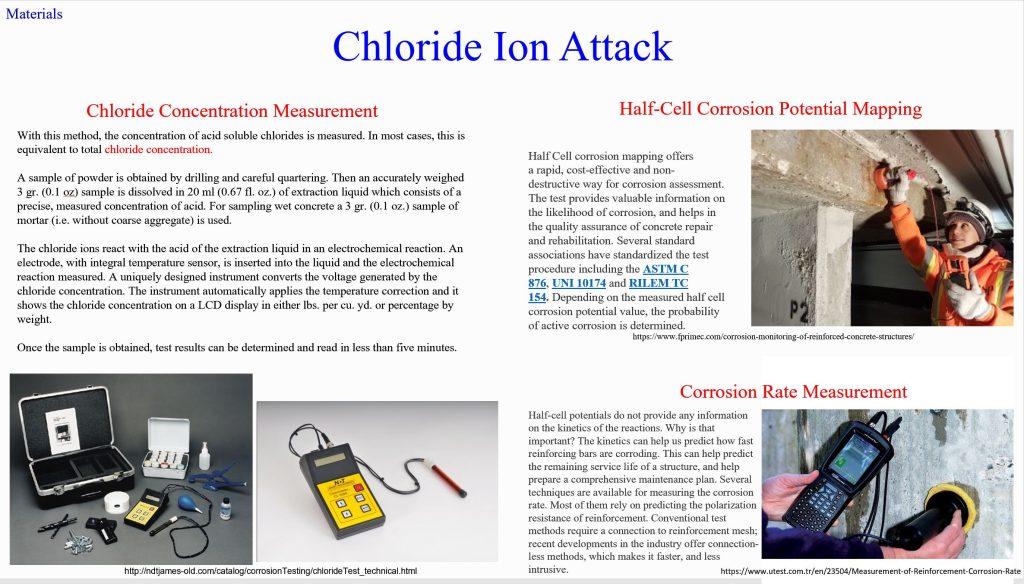