Watertightness
- Introduction
- Causes of Defects
- Good Practices
- Standards
- Maintenance and Diagnostics
- Remedial
- Similar Cases
- References
Maintenance and Diagnostics
Regular inspections and checking should be hence carried out periodically at regular intervals to detect these defects and to take remedial action to remove these defects. An efficient inspection system should be adopted to ensure the conduct of regular checks such as visual inspections periodically.
Maintain or replace integral seals in window units within the duration of the service life in accordance with ASTM E2266-11. Check the condition of windows and caulk seals annually in accordance with ASTM E241-09e1. Maintain repair records to identify a pattern of leakage; and to identify if repairs may be causing or contributing to current leakage. Use of maintenance records to diagnose buildings with chronic leakage problems (e.g., areas that have been subjected to several attempts at remediation). Suspected water leakage in glazing systems should be evaluated using the relevant parts of ASTM E2128-17. NDT methods can be used (e.g., thermography, fiberscope, elastic recovery meter).
Carry out regular maintenance of the fenestration product and its interfaces with the wall system to ensure water penetration resistance in accordance with ASTM E241-09e1 or equivalent. Clean glazing system’s exterior surface to control accumulation of environmental pollutants, as well as to avoid staining
and disfiguration of glass. Periodic maintenance should be carried out as recommended for window
gasket seals and operating hardware in accordance with ASTM C1401-14 or equivalent.
Use cleaning solvents in strict accordance with solvent manufacturer’s instructions and applicable codes, safety regulations, and environmental regulations. MEK (Methyl ethyl ketone) and similar solvents
may damage organic sealants, gaskets and finishes used on fenestration products in accordance
with ASTM E2112-19C, BS 8213-4 or equivalent.
Diagnostics of Defect (see also NDT)
Finding the source of water ingress into the facade system is most crucial. The following methods are recommended:
Thermography can be used to identify the position of cracks. A range of crack widths, representing mechanical damage, has been induced under controlled laboratory conditions. The method is based on the characteristics of heat flow phenomenon, in a conductive medium of specific geometry, which is intended to model predetermined boundary conditions.
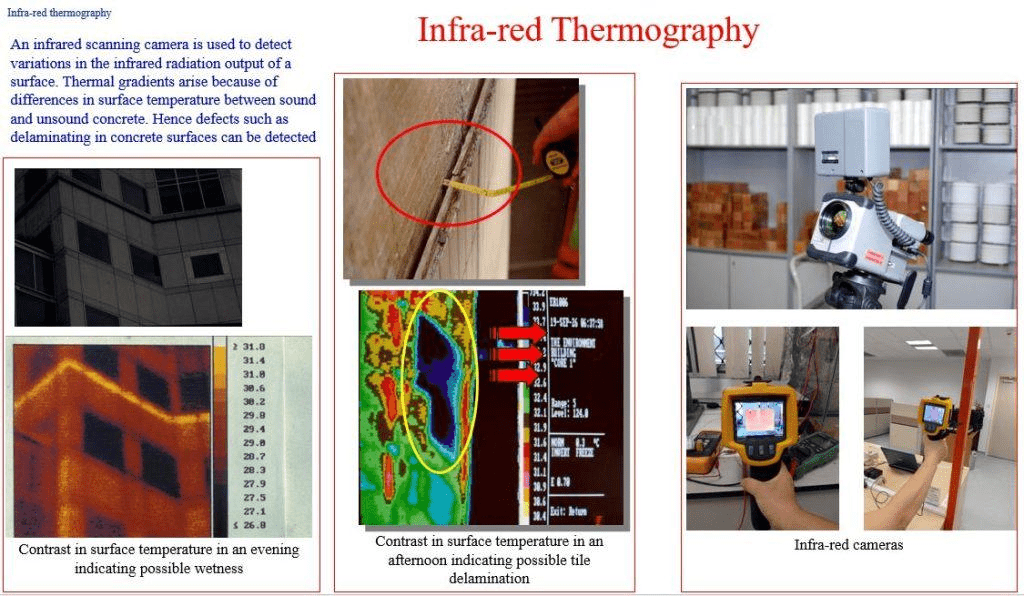
Microwave tomography is a technique to measure the moisture of various materials based on the relatively high dielectric constant of “water” in comparison to the dielectric properties of the material. An electrical field (microwave) is applied to the material, and the microwave induces oscillations of bipolar molecules (i.e., water). Water molecules will reflect and absorb an electrical field during oscillations. A higher electrical field reflected indicates higher water content.
The technique is non-destructive and applicable to wood, brickwork and concrete. The uniqueness of this technique is its ability to measure moisture content at various depths up to 110 mm, allowing the plotting of a 3-D contour of moisture content and facilitating the tracing of the water source.
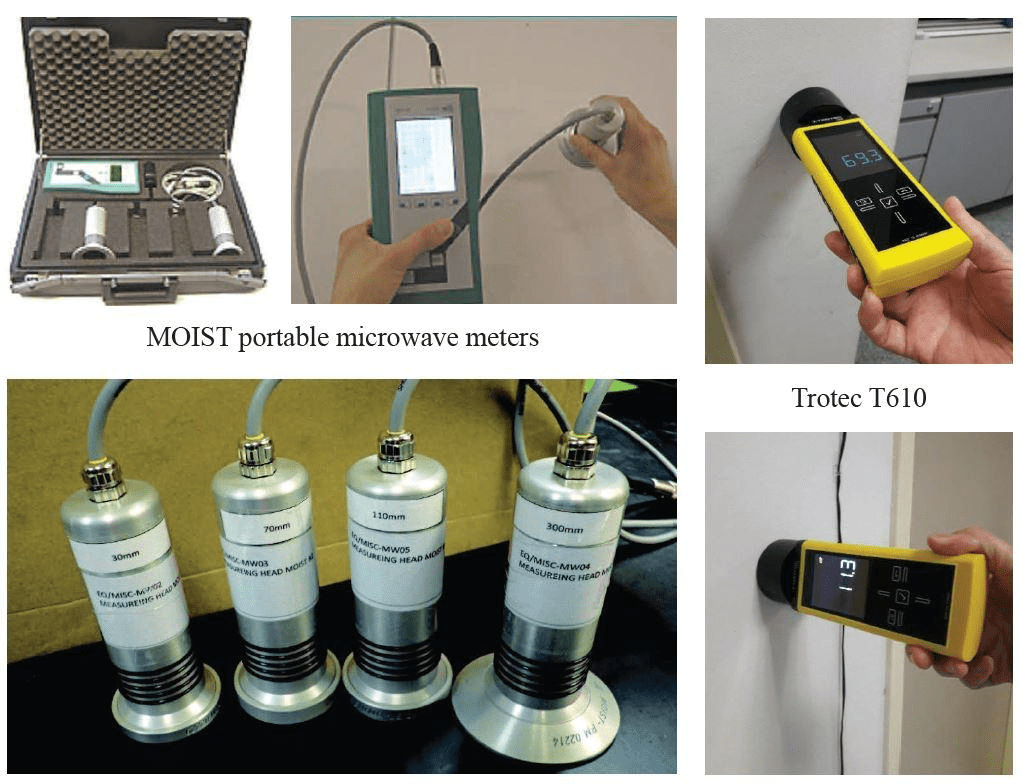