Case 1
- Introduction
- Causes of Defects
- Good Practices
- Standards
- Maintenance and Diagnostics
- Remedial
- Similar Cases
- References
Maintenance and Diagnostics
Adopt ASTM C1193-16 or equivalent to identify areas with remedial sealant repair or maintenance work, as multi-storey structures require a periodic façade inspection at an interval of about 5 years. Replace failed sealants immediately in accordance with ASTM C1401-14, BS EN 13022-1 or equivalent. Test suspected failure of waterproofing using ASTM C1521-19, BS EN 15651-1 or equivalent. Use ASTM C1487-19 or equivalent for remedial work for glazing sealant.
Masonry requires periodic maintenance to ensure its continued successful performance.
Although the brick units are quite durable over time, other materials in the wall system will require periodic repair and/or replacement.
Typical maintenance items which should be addressed are repairing of cracks in masonry, cleaning clogged weepholes, removing stains and efflorescence, repainting steel, replacing caps or copings, repointing mortar joints (tuck-pointing), replacing deteriorated sealants and caulking, and cleaning the masonry.
Diagnostics of Defect (see also NDT)
Thermography can be used to identify the position of cracks. A range of crack widths, representing mechanical damage, has been induced under controlled laboratory conditions. The method is based on the characteristics of heat flow phenomenon, in a conductive medium of specific geometry, which is intended to model predetermined boundary conditions.
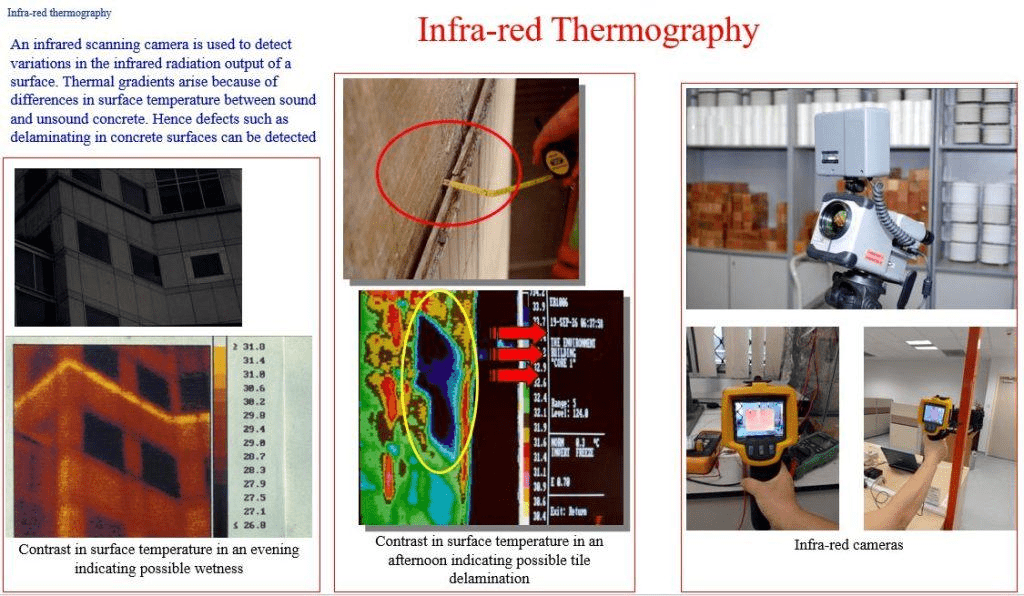
Elastic recovery meter

Sealant deterioration can be determined by the use of Elastic Recovery Meter (INERT)