TiO2 Coating
Good Practices
Apply on newly built substrates
As suggested by suppliers, there is a high possibility of successful performance of TiO2 self-cleaning coating if it is applied on newly built substrates. The possibility of success decreases when the substrate deteriorates with time because the adhesion level of the coating declines. Thus, newly built substrates are appropriate to achieve better adhesion of TiO2 self-cleaning coating39.
Scratch Test at the Design Stage of coating
The functional behaviour of a coating is critical to its adhesion to the substrate. Scratch test is one of widely used, fast, and effective methods to obtain the critical loads that are related to adhesion properties of coating. For all practical application, scratch test can be performed to obtain the critical load as a useful adhesion parameter for evaluation of coatings to ensure their fitness for use. As shown in Figure 6, the CETR-Universal Materials Tester (CETR-UMT) is a unique test and measurement system that can be used for Scratch Testing. CETR-UMT can perform advanced scratch tests (Constant load, Progressive, 3D, X-Y, Angular, etc.) to evaluate the adhesion properties of coating40.
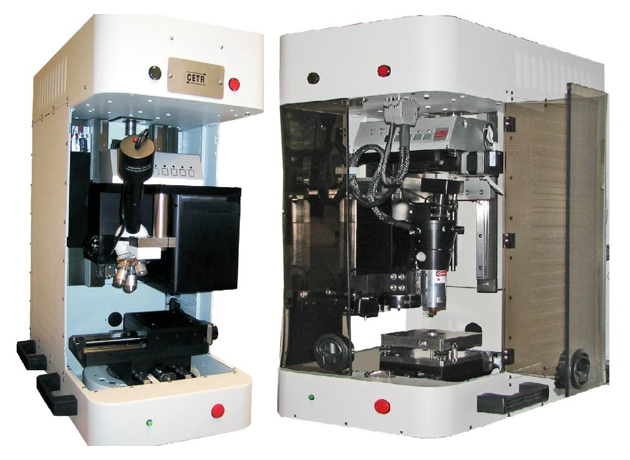
Figure 6 CETR-Universal Materials Tester (CETR-UMT)
(Source: Kuiry, 2012)
A major concern for the manufactures of nano coatings will be to ensure a highly significant scratch/mar resistance level. Nano scratch testing is an ideal tool to measure scratch/mar resistance of the nano coating on each individual substrate. It is important for the manufacture to understand and monitor at what level marring can occur. Marring damage not only affects visual appearance but can lead to full adhesion failure as environmental conditions access through cracking. The scratch testing method is a very reproducible quantitative technique in which critical loads at which failures appear are used to compare the cohesive or adhesive properties of coatings or bulk materials (see Figure 7). During the test, scratches are made on the sample with a sphero-conical stylus (tip radius ranging from 1 to 20m) which is drawn at a constant speed across the sample, under a constant load, or, more commonly, a progressive load with a fixed loading rate. Sphero-conical stylus is available with different radii (which describes the “sharpness” of the stylus). Common radii are from 20 to 200m for micro/macro scratch tests, and 1 to 20m for nano scratch tests. When performing a progressive load test, the critical load is defined as the smallest load at which a recognizable failure occurs. In the case of a constant load test, the critical load corresponds to the load at which a regular occurrence of such failure along the track is observed. In the case of bulk materials, the critical loads observed are cohesive failures, such as cracking, or plastic deformation or the material. In the case of coated samples, the lower load regime results in conformal or tensile cracking of the coating which still remains fully adherent (which usually defines the first critical load). In the higher load regime, further damage usually comes from coating detachment from the substrate by spalling, buckling or chipping38.
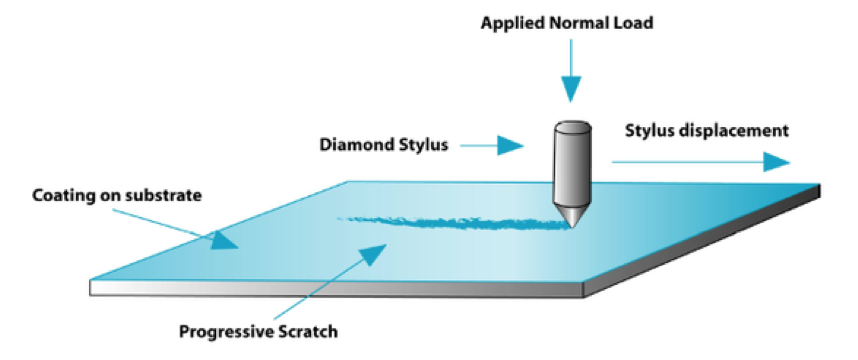
Figure 7 Principle of Scratch Testing
(Source: Leroux, 2010)
Orientation of façade
Orientation of facades affects the sunlight intensity received by the TiO2 coating. Orientation with lesser amount of sunlight intensity results in decrease in photocatalytic activity. TiO2 coating should be installed in orientation with the maximum amount of solar energy received. Common orientation with maximum sunlight would be east-west orientation, however it is dependent the context of the environment.
Level of coating
The different levels where TiO2 coating is applied affects the sunlight intensity being received onto the surface of the coating. Lower levels tend to have lesser amount of sunlight received, whereas higher levels tend to receive higher amount of sunlight. Building owners needs to take into consideration regarding the different levels where TiO2 coating should be placed. It is recommended for TiO2 coating to be placed on levels with higher amount of sunlight intensity.
Design of Column
It is better to have a straight column to allow rainwater to flow off evenly so as to remove the dirt particles and for photocatalytic activity to take place on all areas of the TiO2 coating.
Minimise usage of organic admixtures for cementitious materials
Regarding the characteristics of off-form concrete material, the use of organic admixture for concrete and other cementitious materials must be minimised to avoid possible reduction of the photocatalytic activity. This is because the TiO2 could decompose the organic admixtures in the concrete itself and create large pores on the surface. As a result, the self-cleaning effect may also be limited due to the physical anchoring of the dirt in large pores created6.
Preparation of Site Area before Application
Through Figures 8 and 9, the method used to clean Case Study A’s façade surface is not enough as preparation of site before applying TiO2 as the site area has been exposed to dirt and dust for 7 years, which amounts to a substantial amount of dirt and dust on the exterior façade41. The best site preparation for applyingTiO2 on exterior facades is to jet wash the surface before application41.
The cleaning of building surface before application of TiO2 is important, as this will affect the effectiveness and performance of the TiO2 layer, in terms of its durability. Existing buildings today have been exposed to the environment for a period of time, and that dust and dirt will gather on the building surface. When this happens and the building surface is not cleaned thoroughly, and the TiO2 layer is applied, the TiO2 layer will be bonded with the dust and dirt layer instead of the building surface. Over time, through weathering processes the dirt layer will eventually be removed from the building surface, which leads to the TiO2 layer being removed. Hence, the durability of the TiO2 layer is not as effective as it is supposed to be, and this will affect the performance of the TiO2 layer on the building surface41.
Testing the Spray Guns
Before spraying, fix the cup and fill the cup half full with deionized water or tap water. Attach the hose and turn on the compressor. Gently press the trigger half way. It will be noticed that only air is coming out of the spray gun’s nozzle but no water or mist yet. Next, gently press the trigger all the way for the mist to be out of the spray gun’s nozzle. Practice spraying at some plastic sheets or newspaper at a minimum distance of between six to ten inches. The optimum distance to spray is 12 inches. They spraying distance will vary due to many factors. The factors include air pressure of the compressor, setting of the spray gun, wind and others. Always spray at right angle to the surface (Figure 8) and do not swing the air gun at a curve (Figure 9)39.
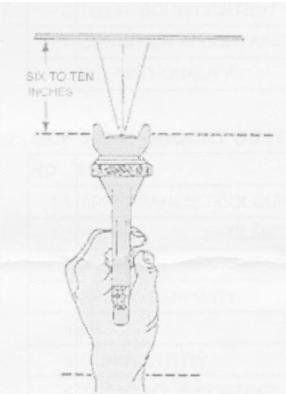
Figure 8 Spraying at right angle
(Source: Guan, 2013)
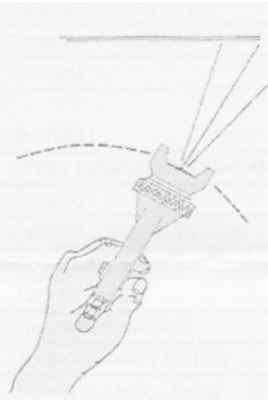
Figure 9 Spraying at a curve
(Source: Guan, 2013)
Also, air gun should not be tilted at an up or down angle while spraying (Figure 10) because this will cause an uneven coating where some areas will be thick and wet, whereas other areas will be thin and dry39.
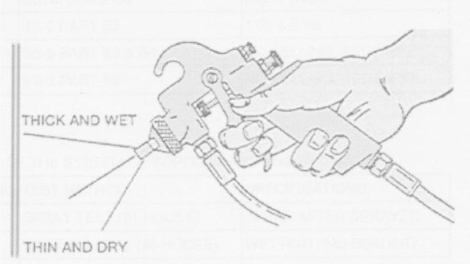
Figure 10 Tilting of air gun
(Source: Guan, 2013)
Interior UV emitters
When TiO2 is applied indoors, there is little or no source of sunlight most of the time, therefore UV emitters should be used indoors to ensure that the TiO2 surfaces perform well41.
Take note of building surroundings
When applying TiO2 to the exterior of buildings, it is important to take note of the surroundings, whether or not there are obstructions in the area that minimizes the UV radiation exposure and also rain from washing away the broken down dirt and stains.
Coat the top of the façade with TiO2
For Case Study A, the TiO2 test was rendered ineffective because the top of the façade was not coated withTiO2 and the dirt from the top of the façade will be carried down through rainwater pattern, which resulted in streaking41.
Avoid Usage of Sunshades/ solar panels
Presence of sunshades or solar panels blocks off rainwater flow, resulting in uneven rainfall distribution on the TiO2 coating; irregular cleaning effect observed on facades. It is better not to have sunshades or solar panels attached on the façade if TiO2 coating is in place. This is to allow equal rainfall distribution to reach all the areas of the coating for self-cleaning function to take place. In the presence of sunshades or solar panels, the runoff pattern is disrupted where rainfall are unevenly distributed onto the surface. Uneven distribution of rainfall results in uneven performance of self-cleaning effect. This effect is known as irregular cleaning effect where only certain patches of TiO2 coating performed its self-cleaning ability. Areas that received rainfall are cleaned, but spots that did not receive rainfall will not be clean. Different patches of dirt stains will be observed on the glass panel. This effect is illustrated in Figure 11, which these previous projects with solar panels and sunshades resulted in irregular cleaning effect, where façade was in a worse condition than non-coated buildings.
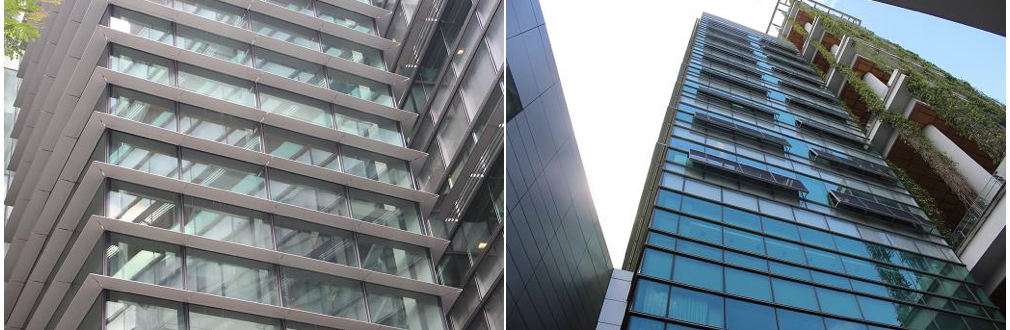
Figure 11 Sunshades (left) and solar panels (right) installed on glass façade
(Source: Law, 2016)
Avoid Protruding features
Protruding features such as protruding roofs are likely to influence the rainfall distribution, which in turns affects the photocatalytic activity. Dirt staining and sealant staining may be observed on areas where self-cleaning function did not take place due to inadequate rainfall. Design considerations should avoid protruding roofs, so that even rainfall distribution is expected on the surface of TiO2 coating.
Incorporating maintenance from design stage
Incorporate maintenance factors into building design and material selection process is necessary for the maintainability of façade coatings.
Contact Angle of Water on Building Surface
The contact angle of water on building surface would also affect the performance of TiO2, thus the closer the contact angle of water source to the solid surface should be 0 degrees. Building walls are most commonly built to be vertical or sloping to the ground, however there are buildings that are uniquely designed specific to the function of the building, such as the unconventional facades shown in Figures 12 and 13 wherein theTiO2 contact with water is close to non-water-repellent. Thus, when applying TiO2 on the surface of these façade types, it will be difficult to ensure that there is a fine thin layer ofTiO2 film on the surface and that all areas of the curved surface will be exposed to sunlight. Therefore, impacting the contact angle of water on these curved surfaces affects the hydrophilicity property of the TiO2 layer41.

Figure 12 Case Study B (left) Figure 13 Case Study C (right)
Usage on suitable materials
Different substrate materials affect the adhesion process of the TiO2 product on the substrate surface. surfaces that are non-porous and has a smooth surface is more effective than surfaces that are of irregular textures and are porous (i.e. glass). This is due to the fact that when TiO2 is applied to porous surfaces, it is common that the pores are filled with dirt that have been accumulated over the years, hence applying the TiO2 on the such surfaces would not yield the performance that consumers are expecting. This is because there is dirt in the pores, which are very difficult to remove, hence there is a possibility that the TiO2 layer is not as efficient as the consumer had expected). TiO2 is also more suitable for substrate materials that are smooth and non-porous in order that adhesion of the substrate surface is well bonded. Some widely examples of suitable substrate materials are glass and aluminium. Other substrate materials that are less suitable are concrete and stone surfaces due to their opposite properties, being coarse and porous which impedes the performance of TiO2.
Reduce Proximity to landscapes
Proximity to landscapes is likely to result in algal growth on the façade. As TiO2 coating is unable to perform self-cleaning function on algal growth, it affects the aesthetics and incurs rectification cost on building owners. Designers should avoid application of TiO2 coating on facades that is near to landscapes, or distance should be kept to avoid algal growth on facades. This section of Case Study D is highly shaded due to adjacent building blocking off sunlight (Figure 14). At times of rainfall, proximity of building deters rainfall from falling directly onto the coating. Regular flow off pattern is disrupted due to protruding roof. Insufficient sunlight intensity is evident from the shading of adjacent building. With insufficient sunlight and rainfall, photocatalytic activity is expected to decrease. Minimal sealant and dirt staining were evident on the area being shaded off by the building (Figure 15).
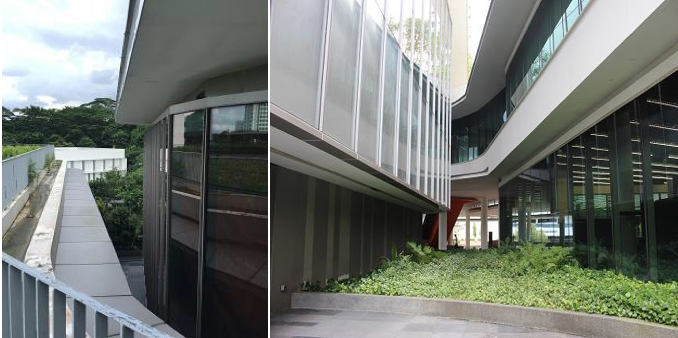
Figure 14 Height of adjacent building blocking Case Study D
(Source: Law, 2016)
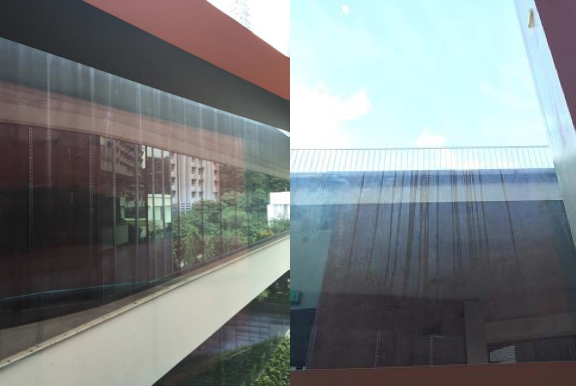
Figure 15 Sealant (left) and dirt staining (right) observed on glass façade
(Source: Law, 2016)
For Case Study E (Figure 16), there are no surrounding buildings blocking sunlight and rainwater on the coating. Performance of coating is satisfactory with no stains observed on three orientations of the facade (Figure 17). This highlights that TiO2 coating should be applied on areas with optimal exposure of sunlight and rainfall for optimal performance44.
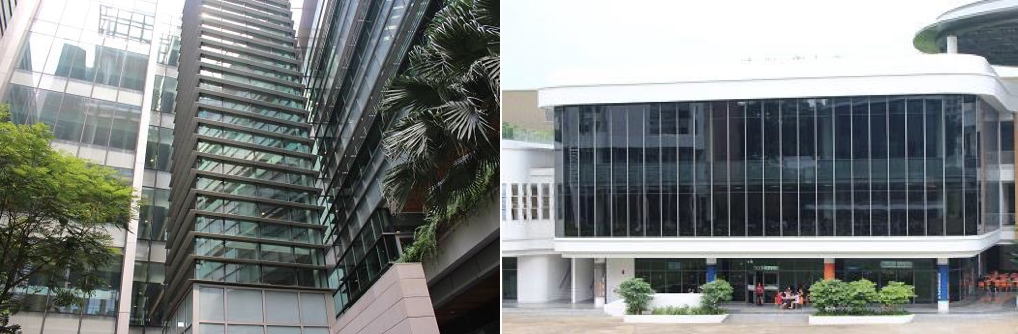
Figure 16 Recessed building shape (left) as compared to regular shaped building (right)
(Source: Law, 2016)
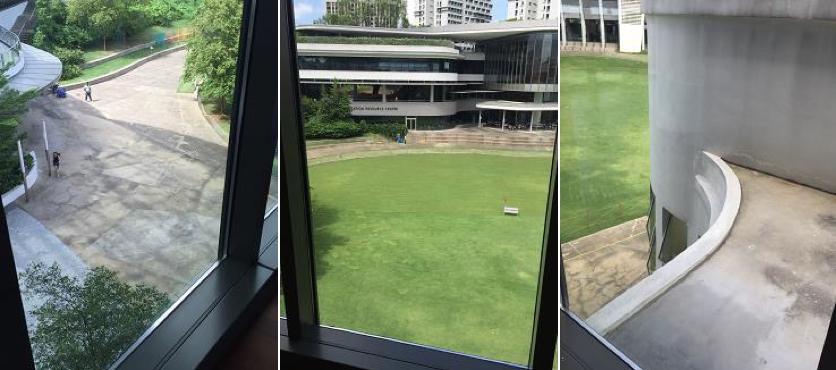
Figure 17 Optimal performance of TiO2 coating on NS (left), EW (middle) and NS (right) orientation
(Source: Law, 2016)
Accessibility for maintenance
Maintenance for façade should be provided even if TiO2 coating is applied, as maintenance is still needed for TiO2 coating to perform efficiently. Even if the frequency of maintenance is dependent on the supplier, however, 2-3 times in 5 years is an optimal maintenance period44.